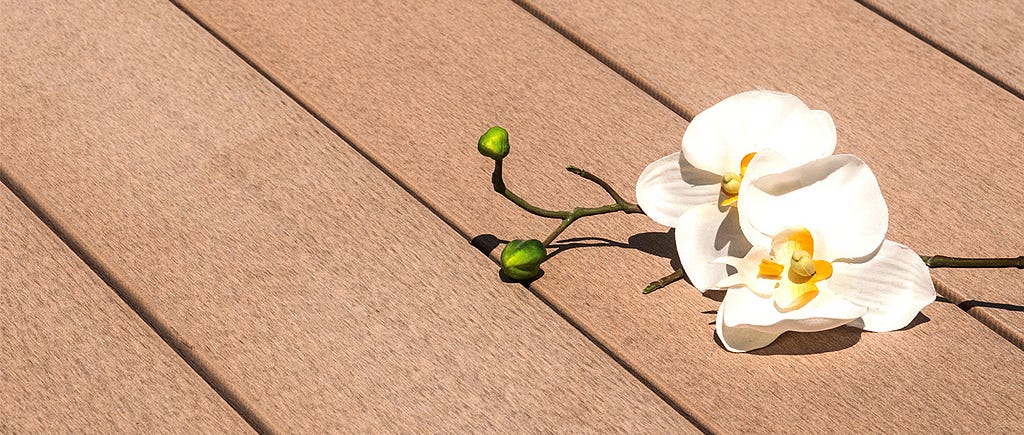
- Dance to your own music and take some risks in life, because it is often the risk taker who changes the course of history and contributes to the well-being of millions of lives.
- At SFO we have always pioneered to change the history of humans and hence Market Economy, Progress, Growth, Development, (MEPGD) has always been a way of life in SFO.
- Because human history changes when the quality of life of people changes.
- And so far GDP ( at household level or state level or national level or continent level or world level ) has been the biggest GROWTH ENGINE for uplifting human life.
- TRUTH is that GDP grows by way of creation of capital assets.
- When it comes to creating capital assets we don’t shy of creating capital assets as GROWTH ENGINES.
- Our new GROWTH ENGINE is COMPOSITES.
- Composites are projected to replace the 2.5 Tn metals market.
- Composites are also projected to replace the 0.5 Tn woods market.
- We invite supply chain partners for our New Growth Engine.
- Together we can build back better. Stay safe and stay healthy.
The Global Composites Market Overview
The global Composites market size is expected to gain market growth in the forecast period of 2020 to 2025, with a CAGR of 4.8% and will expected reach USD 200 Bn by 2025, from USD 115 Bn in 2019.
- In 2019, the volume of the global composites market reached 11.8 million tons valued at 115 Bn USD.
- The market volume, is expected to reach 15.9 million tons by 2025 valued at 200 Bn USD.
- The average year-on-year volume growth rate throughout the period between 2019 and 2025 is expected to be roughly 4.8 percent.
The Indian Composites Market Overview - Government plans to develop a furniture cluster
- Furniture making is one area where the government is aiming to kill many birds with single stone. Under the ‘Atmanirbhar Bharat Mission’, the government is working to develop a furniture cluster near a port where common facilities for testing, research, design and packaging can be provided. Such a cluster would help furniture manufacturing on a large scale to meet domestic requirements and push India into the global furniture trade market.
- The government is also planning to tighten the restrictions for the import of furniture into the country as part of its Aatmnirbharata (self-reliance) policy. This move will not only save foreign currency but also will boost the domestic industry and generate employment as furniture and wood panel industry are labour intensive. According to available data, India’s annual imports of wood and allied products amounted to Rs 15,000-20,000 crore while furniture or wood panel are not technology intensive products. Moreover, several countries are considering reducing dependence on China, which could benefit India’s wood panel industry, especially in MDF exports.
- Further, global trade in furniture is about Rs 20 trillion and India is not a key player in this segment despite having cheap labour in abundance. Further, the government is working on the possibility of importing wood in India without any duty, which would help solve the issue of availability and boost the domestic furniture manufacturing industry.
- The size of the organized furniture market in India is about Rs 25,000 crore, while the overall furniture market size in India about Rs 2 trillion. Furniture imports from China into India are currently estimated at US$2 billion. With anti-Chinese sentiment prevailing in the country now, the wood panel industry and the furniture makers in India expect a big opportunity for Indian modular furniture makers in replacing these Chinese imports over medium to long term. According to them, there is likelihood of an increasing acceptance of ready-made furniture or modular furniture in India which would also drive higher demand.
The Composites World
- The manufacturing world likes to think of composites fabrication as a single, global entity that operates to serve its customers’ needs with a variety of highly engineered parts and structures. In reality, however, the composites industry is an amalgamation of many highly vertical markets — aerospace, automotive, marine, consumer, wind, etc. — that consume composite materials in a variety of different ways. This usage is driven by part performance requirements, cost thresholds, regulations and customer demand. For instance, the material, process and cost parameters in commercial aerospace manufacturing are substantially different than the material, process and cost parameters in recreational boatbuilding.
- Composite materials can meet such diverse needs because they are so diverse themselves. The array of fiber, resin, tooling, process and finishing options available make possible the fabrication of nearly any composite part for nearly any application. Couple this with the tremendous strength, stiffness, durability and light weight attributes that composites offer and it’s not hard to understand why use of these materials is growing as much as it is.
- The highly bespoke nature of composites not withstanding, there are some broad materials and process trends shaping the entire composites industry that bear watching over the next several years. First among these is the effort to get touch labor out of the manufacturing process by increasing use of robotics and automation. This is driven by several things, including a desire to increase consistency and quality, a desire to reduce costs, and a demand for higher volume manufacturing.
- Second is the effort to get out of the autoclave. As wonderful as the autoclave is at consolidating composite laminates, it is expensive to acquire and operate. It also can be a production bottleneck that hinders the drive toward higher volume throughput. As a result, out-of-autoclave (OOA) materials and processes — resin infusion, resin transfer molding (RTM) and thermoplastic composites — are being considered more seriously in a range of applications, not the least of which are large commercial aerospace structures.
- Third, thermoplastics in general are on the rise, primarily because of the attributes they offer, including OOA processing, easy storage and handling (compared to prepregs) and easy recycling.
- Fourth is the advent of Composites 4.0, the composites industry’s version of Industry 4.0 — the complete digitization of the manufacturing process, from design to simulation to manufacturing simulation to manufacturing to troubleshooting to part tracking and much more. This is leading to development and use of complex algorithms that will govern thinking machines in the next-generation composites manufacturing environment.
- Fifth is the massive expansion of additive manufacturing (AM) in composites fabrication. The initial use of chopped fiber reinforcements in thermoplastic-based AM has led to the use of continuous fiber reinforcements to make discrete parts as well as tooling and mold components. The industry has also seen the advent of thermoset-based AM as well as new processes that combine AM with automated fiber and tape placement.
- All of these technologies spring from and help drive a highly dynamic and fast-changing composites industry, and in the Multitude of Markets that follow. Here we shall see how composites materials and processes are being adapted and applied in each of the major end markets served by composites designers and fabricators. We will also see how macro trends in each end market affect the composites manufacturing community.
Aerospace
- Aerospace composites: Some of the newest aerocomposites manufacturing technologies are being deployed in the manufacture of the wings for the Boeing 777X. The wingspan of the plane is 235 ft (72m) and the wings are being fabricated with autoclave-cured carbon fiber prepreg at a Boeing facility in Everett, Wash., U.S. The plane is expected to enter service in 2020.
- In 2019, the global commercial aerospace industry was shaped and dominated by the grounding of the Boeing 737 MAX, which was precipitated by the crash of two 737 MAX aircraft, one in late 2018 and the other in early 2019. The cause of the crashes, which killed more than 300 people, was an automated flight control system Boeing developed specifically for the 737 MAX. Boeing has committed significant resources to correcting the automated flight control system, but as of this writing in early Novembermid-October 2019, the plane was not expected to return to service until late 2019 or early 2020. In the meantime, Boeing continues to assemble 737 MAX aircraft, but is not delivering these until the fix is done, proven and certified.
- The grounding of the plane has had significant ripple effects throughout the aerospace industry supply chain, with some consequence to the composites industry as well. In particular, Boeing has had on the drawing board for some time the New Midsize Aircraft (NMA), a twin-engine, twin-aisle, mid-range plane that would fit between the 737 and the 787 in terms of size and range and would serve a segment that used to be occupied by the discontinued 757. Initial speculation said Boeing would announce the NMA at the 2019 Paris Air Show, with entry into service around 2025. However, the 737 MAX grounding apparently has not allowed the company to devote significant resources to a new program launch, plus Boeing experienced problems with the engine on the 777X and delayed first flight of this craft (with all-composite wings) to early 2020. All of this added up to no NMA announcement in Paris.
- The NMA program is also complicated by Airbus, which announced at the 2019 Paris Air Show the A321XLR, an extended version of the single-aisle A320. It will seat 240 people and have a range of 4700 nautical miles. This makes the A321XLR competitive with the NMA, for which Boeing is contemplating two versions: One that seats 225 with a 5,000-nautical-mile range and another that seats 275 with a 4,500-nautical-mile range. If Boeing announces the NMA soon after the 737 MAX returns to service, and assuming both of these things happen by mid-2020, then prospective customers would have a choice of two aircraft that offer similar passenger and range options, with comparable efficiency, with one a single-aisle and the other a double-aisle configuration.
- The NMA is significant because it represents the next all-new aircraft program on the horizon, and, like the Boeing 787 and 777X, and the Airbus A350, it is expected to feature major structures fabricated with carbon fiber composites. In addition, beyond the NMA, just over the horizon, are expected single-aisle replacements for the Boeing 737 and the Airbus A320. Both of these aircraft are ripe for conversion to carbon fiber composites and would represent a major leap forward in composites manufacturing throughput — Boeing and Airbus both anticipate single-aisle replacement build rates of 100 shipsets per month. These programs could, if announced in the next couple of years, enter service in the 2028–2030 window.
- The 737 MAX grounding, however, has thrown some uncertainty into this timeline. That is, Boeing could decide that a 737 replacement should be accelerated, and launch its development sooner than planned. Such a decision could, consequently, prompt Airbus to move up its A320 replacement, which is likely that company’s next all-new aircraft. In short, as long as the 737 MAX is grounded, there is much uncertainty in the commercial aerospace supply chain in general, and the aerocomposites supply chain in particular.
- Setting aside the issue of which aircraft programs might be announced when, there are substantive and unanswered questions surrounding the NMA and single-aisle replacements. The overarching question is if and where composites will be used on these planes. For the twin-aisle NMA, use of composites is almost certain, particularly given the supply chain and manufacturing processes in place for the 787, 777X, and the A350. Also important is the fact that the air carriers themselves prefer the durability and ease of maintenance of composite structures compared to traditional aluminum structures — this fact in and of itself might be enough to compel continued use of composite materials in large aerostructures, regardless of size or configuration.
- Assuming that carbon fiber composites use in large aerostructures will continue, the next question is what type of materials those will be. The incumbent material and process (M&P) combination is autoclave-cured carbon fiber/epoxy prepreg, laid down for the most part via automated tape laying (ATL), automated fiber placement (AFP) or by hand. However, the M&P combinations qualified for the 787 and the A350 in particular are relatively old, having been developed in the early 2000s.
- Still, the fact that these M&Ps are qualified gives them a leg up against newer M&Ps, which are still being developed and qualified. And for the NMA, for which Boeing likely does not want to develop significant and new M&Ps, the incumbent technology likely wins out. Further, the build rate of the NMA is likely to be similar to the build rate of the 787 (124/month) and the A350 (10/month);, thus there is less pressure by Boeing to develop and qualify faster-cycling M&P technologies.
- All of these assumptions, however, go out the window with the single-aisle replacements that will follow the NMA. Boeing’s and Airbus’s current single-aisle aircraft, the 737 and the A320, are the aerospace industry’s best and most profitable sellers and most profitable. Manufacture of composite parts and structures for these planes at the anticipated rate of 100/month is not feasible using current autoclave cure technology. Because of this, the new single-aisle planes in development will almost certainly employ out-of-autoclave (OOA) materials and processes that deliver dramatically shorter part cycle times.
- This has thrust to the fore several OOA technologies that are almost certain to be deployed extensively in next-generation aircraft. These technologies include thermoplastic composites, resin infusion and resin transfer molding (RTM). Boeing and Airbus each are pursuing these technologies through a variety of research and development programs designed to bring maturity to a technology readiness level (TRL) that allows commercial deployment by 2025 at the latest.
- Airbus, for its part, is pursuing a variety of solutions through multi-company, high-profile programs. Most notable is the Wing of Tomorrow Programme, being led by GKN Aerospace (Shirley, Solihull, U.K.), with the National Composites Centre (NCC, Bristol, U.K.), Northrop Grumman (Clearfield, Utah, U.K.), Spirit AeroSystems (Wichita, Kan., U.S.) and Solvay Composite Materials (Alpharetta, Ga., U.S.). This program is assessing use of RTM to fabricate wing skins, wing spars, ribs, and wing box. GKN announced at the 2019 Paris Air Show that it had produced demonstrator parts for Wing of Tomorrow, followed in October by the news that it had delivered a demonstrator tool.
- The Wing of Tomorrow’s goal is to develop a very high-rate commercial aircraft wing structure manufacturing process that is, in nearly every measurable way, an order of magnitude better than current wing manufacturing technology. This means better automation, fewer parts, better parts integration, faster cycle time, faster NDI and faster assembly. Testing of a full wing is expected to begin in 2021.
- Infusion of wing structures is not novel. Two commercial aircraft already use the process: The Airbus A220 and the Irkut MC-21, both single-aisle aircraft. The A220 was developed by Bombardier as the CSeries and then sold to Airbus in 2018. Its infused wings are still fabricated by Bombardier at its Belfast, Northern Ireland, facility, which Bombardier put up for sale in 2019 (Spirit AeroSystems announced in October 2019 that is acquiring Bombardier’s Belfast operations). The Irkut MC-21 is being manufactured by United Aircraft Corp. (Moscow, Russia) for the Russian market. Its wings are fabricated by AeroComposit (Moscow) using a Solvay Composite Materials single-component resin system. What the A220 and the MC-21 prove is that infusion is feasible for commercial aircraft, but the rate on both of these planes is relatively low. The technology must now be matured for a high-rate environment.
- Thermoplastic composites, for their part, are being targeted toward fuselage structures. This is important because for many years it was unknown if composite materials made sense for use in the fuselage of a single-aisle aircraft, primarily because fuselage skin thickness on a single-aisle is thinner than that on a twin-aisle aircraft. That thinner skin, using incumbent composite materials and processes, makes composites cost- and weight-prohibitive. The challenge, then, is to develop a composites M&P combination for the fuselage that provides relatively thin and affordable skin thickness.
- In Europe, this effort is being funneled through the Clean Sky 2 Next Generation Multifunctional Fuselage Demonstration (MFFD) project. As the name implies, the program aims to increase integration of fuselage, systems, cargo and cabin elements, in the process minimizing the use of fasteners. Use of thermoplastics would allow this via welding. One of the most active companies in the development of thermoplastic aerostructures is GKN/Fokker (Hoogeveen, Netherlands), which at JEC World 2019 in Paris exhibited a thermoplastic fuselage panel fabricated for Gulfstream. It features an interconnected, welded grid structure that exemplifies the multifunctionalism envisioned by Clean Sky’s MFFD. The Fokker structure represents a small step of many to come in the maturation of this technology for potential use in a single-aisle commercial aircraft.
- Beyond the fuselage, thermoplastic composites are already making significant inroads with aircraft already in service. Boeing in particular is in the midst of a concerted effort to convert smaller structural parts (brackets, clips, fasteners) from thermoset to thermoplastic composites. Thermoplastics specialists like ATC Manufacturing (Post Falls, Idaho, U.S.), which specializes in continuous compress molding, are leading this conversion effort.
- Activity is also significant on the raw materials side of thermoplastics. Resin manufacturer Victrex Plc (Cleveleys, U.K.) made waves in the composites industry with the introduction of PAEK AE 250, a line of carbon fiber tapes and laminates prepregged with its low-melt polyaryletherketone (PAEK) resin. PAEK offers a melt temperature of just 305°C — compared to 350° for polyetheretherketone (PEEK), a mainstay in thermoplastic aerocomposites. This is important because reduced melt temperature speeds the heating/cooling cycle and allows for fast cycle times. It also enables overmolding of PEEK functionality (ribs, attachment clips) onto PAEK laminates.
- Anticipating increased demand for thermoplastics in aerocomposites, Solvay Composite Materials announced in September 2019 that it is expanding production capacity at its Anaheim, Calif., U.S. facility. The plant makes unidirectiitonal (UD) carbon fiber tapes prepregged with PEEK, PEKK or PAEK resins. The expansion, combined with ongoing process optimization efforts, will increase capacity at the facility fourfold since 2016.
- Also on the fuselage front, but back in the thermoset realm, Spirit AeroSystems introduced at the Paris Air Show 2019 its newly developed Advanced Structures Technology and Revolutionary Architecture (ASTRA) fuselage panel for a single-aisle aircraft. It’s autoclave cured using a new fuselage design Spirit developed called “sheet stringer technology.” The company says ASTRA offers cost savings of 30% compared to incumbent architectures and production approaches and can meet a rate of 60 shipsets/month. Further, physical testing showed that ASTRA met all of the strength and stiffness requirements of a single-aisle aircraft.
- Similar to Spirit, although on a smaller scale, was MTorres (Torres de Elorz, Navarra, Spain), which exhibited at the Paris Air Show a rib-stiffened “grid/skin structure,” manufactured via resin infusion of dry carbon fibers. The idea came from Stephen Tsai, composites veteran and professor of aeronautics and astronautics, emeritus, at Stanford University, who designed the ribs in a lattice structure, with each rib a fixed width and height, and spacing between ribs also fixed. The rib architecture uses carbon fiber tapes placed continuously, by MTorres AFP equipment, in one direction (A), and discontinuously in the intersecting direction (B). Then, for the next layer, tapes are placed discontinuously in the A direction and continuously in the B direction. This pattern would continue until the rib’s desired thickness is reached. In this way, each rib joint would always be crossed by a continuous tape. Once the ribs are built in the tool, a skin is laid over it via automated AFP/ATL and the entire structure is co-cured.
- Use of resin transfer molding, infusion, thermoplastics and additive manufacturing in next-generation commercial aerospace structures is being explored.
- The carbon fiber supply chain, meanwhile, has been busy positioning new and existing fibers for next-generation aerospace applications. Toray (Tokyo, Japan), the world’s largest carbon fiber manufacturer, introduced in 2017 its T1100/3960 prepreg, which offers excellent strength and stiffness properties. T110/3960 has been qualified by Spirit AeroSystems. Hexcel (Stamford, Conn., U.S.), for its part, has introduced HexTow HM50, a high-modulus and high-tensile strength carbon fiber. Teijin (Tokyo, Japan), announced in January 2019 that its Tenax carbon fiber and carbon fiber thermoplastic unidirectional pre-impregnated tape (Tenax TPUD) have been qualified by Boeing and registered in its qualified products list. Finally, Hyosung (Seoul, South Korea), in late 2018, introduced a new intermediate modulus, high-strength carbon fiber for the aerospace market, and in June 2019 signed a memorandum of understanding with Saudi Aramco (Dhahran, Saudi Arabia) for the building of a joint carbon fiber manufacturing facility.
- All of this activity, positioning and jockeying of the aerospace supply chain anticipates substantial growth in the commercial air travel market over the next 20 years. Boeing, in June 2019, issued its Commercial Market Outlook 2019–2038. In it, the company estimates that the world will need, over the next two decades, 32,420 single-aisle aircraft, 8,340 twin-aisle aircraft, 2,240 regional jets and 1,040 freighters. Airbus issued its own Global Market Forecast 2019–2038. It divides aircraft into small, medium and large categories, but reaches a conclusion similar to Boeing’s. Airbus anticipates need for 29,724 new small aircraft, 5,373 new medium aircraft and 4,116 new large aircraft, with freight units comprising 855 planes total in the medium and large categories.
- Occupying a small corner of the global commercial air travel market are supersonic aircraft, which have not been in service since the Concorde was retired in 2003. There are several firms now pursuing new supersonic aircraft, and one of the most prominent is Boom Aerospace (Englewood, Colo., U.S.), which is developing the composites-intensive Overture. Boom CEO and founder Blake Scholl, at the Paris Air Show, said that Boom is nearing completion of the XB-1, a subscale prototype of the Overture that is expected to be rolled out by the end of 2019 and test flown sometime in 2020. Overture will have a maximum speed of Mach 2.2, a cruising altitude of 60,000 feet (19,354 meters) and will take passengers (55–75) from Sydney to Los Angeles in just 7 hours, or Washington D.C. to London in just 3.5 hours. Scholl stated that ticket cost on Overture is expected to be competitive, on a seat-per-mile basis, with current airline pricing. Scholl also said that Overture is expected to use a technology called Prometheus Fuels, which converts atmosphere carbon into gasoline or, in Boom’s case, jet fuel, using electricity sourced from renewable resources. In this way, he said, the plane will provide zero net carbon supersonic flight.
- 2019 also saw a small but growing aerospace segment begin to take shape. It’s most broadly called urban air mobility (UAM) and includes a variety of small craft (4–10 passengers) designed to move people in intra and inter-city environments. Aircraft range varies, depending on the size of the craft and its propulsion system, but the goal is to be able to move a few people from one point to another within a major urban area, or from one urban area to another. Uber, which is working on its own eVTOL, requires a range of 60 miles on a charge. Regardless of the range requirements, composites use in eVTOLs is a must, particularly given the dependence on battery power. Because of this, several eVTOL developers (and there are more than 150) are investing heavily in composites engineering talent. The challenge is that the eVTOL market will likely have certification standards as stringent as the commercial aerospace market, but also will require much higher manufacturing volumes that step toward those in automotive. This is driving increased interest in automation and efficiency in composites fabrication processes to drive down cost, boost quality and meet rate. The high level of activity in this market not withstanding, there is still much to be done before eVTOLs begin commercial service. Certification, airspace management, safety standards, take-off/landing locations, and more are yet to be worked out. Commercial service of the first eVTOLs likely will not begin until 2024–2025.
- Another craft within the UAM sector that is set to consume composite materials (for the same reason) is the all-electric commercial airplane. An example of this, introduced at the Paris Air Show 2019, is the Alice, an all-electric, all-composite aircraft developed by Eviation (Kadima-Tzoran, Israel). Alice is a nine-seat regional transport aircraft that has a range of 650 miles/1,000 kilometers at a cruising speed of 240 knots. The plane features one primary pusher propeller at the tail and two additional pusher propellers at the wing tips. The company expects the plane, which has a list price of $4 million, will be certified in late 2020 or early 2021.
- The advent of Eviation’s Alice portends an emerging future for commercial air transport — that of all-electric regional transport. Although the Alice seats only nine passengers, it’s not difficult to imagine the technology behind it evolving to allow a larger craft that can carry more people and fly further — similar to today’s regional jets. As if to prove the point, Boeing and engine-maker Safran announced in September 2019 a joint investment in Electric Power Systems(EPS, Hyde Park, Utah, U.S.), which manufactures electric and hybrid-electric energy storage systems. These would be applied to aircraft propulsion. EPS is the second advanced battery solutions company to join the Boeing HorizonX Ventures investment portfolio, following an investment in Cuberg (Emeryville, Calif., U.S.), a lithium metal battery technology company, in 2018. Safran Ventures also recently invested in OXIS Energy (Abingdon, U.K.), a leader in lithium-sulfur cell technology for high energy density battery systems.
- Airbus, for its part, is developing the E-Fan X, a hybrid-electric aircraft demonstrator. In the test aircraft, one of the four jet engines will be replaced by a 2-megawatt electric motor. The electric propulsion unit is powered by a power-generation system and battery. When high power is required — at take-off, for example — the generator and battery supply energy together. The E-Fan X is expected to make its first flight in 2021.
Automotive
- Automotive composites: Pultruded profiles serve as the load-carrying skeleton for the overmolded, fiber-reinforced PA6 muscle of this next-generation windshield frame that outperforms the current BMW i3 structure. Source | SGL Carbon
The automotive industry continues to develop composites for lightweighting vehicles, driven by fuel economy and emissions regulations:
- Current U.S. corporate average fuel economy (CAFE) standards mandate a fleet average of 54.5 mpg (23.2 km/L) by 2025. (Note: President Trump has proposed scaling back these standards, but as of early November 2019, that scale-back had not been implemented.)
- China’s Corporate Average Fuel Consumption (CAFC) sets a fleet target of 20 km/L by 2020; and
- EU emissions regulations mandate a mere 95 g/km of CO2 by 2021, with another 15% reduction by 2025, and in 2030, a further 30% reduction from 2021.
The market for carbon fiber in automotive applications was estimated at more than 7,000 metric tons (MT) per year by Chris Red of Composites Forecasts and Consulting LLC (Mesa, Ariz., U.S.) at CW’s Carbon Fiber 2017 conference, with more than 100 models currently specifying carbon fiber-reinforced plastic (CFRP) for OEM components. He projects this market will grow to almost 11,000 metric tonnes by 2025.
China is the number one automotive market, producing 27.8 million vehicles in 2018, which includes all passenger cars, light commercial vehicles, trucks, buses and coaches. This is compared to:
- 11.3 million vehicles in the U.S.
- 9.7 million vehicles in Japan
- 5.2 million vehicles in India
- 5.1 million vehicles in Germany
- 4.1 million vehicles in Mexico
- 4.0 million vehicles in South Korea.
Thus, it isn’t surprising that development of composite structures used in actual series production vehicles — not just high-end options or concept/prototype models — is being led by Asia and Europe. Recent composites development announcements in China include:
- CSP VICTALL (Tanshan, China) has announced that Jiangling Motors Corp. (JMC) will use advanced composites for the pickup boxes of its new Yuhu 3 and Yuhu 5 pickup trucks, the first such use of composites in the Chinese automotive industry.
- Kingfa (Guangzhou, China), working with systems supplier Brose Fahrzeugteile (Coburg, Germany), has developed a door module, which uses three types of KingPly organosheets and KingStrong unidirectional tapes, augmented with pultruded PP-LGF injection molding material for ribs and complex surfaces, to cut weight 35% (1 kilogram) for the Ford Focus vs. a PP-LGF 30 door module carrier.
- Magna Exteriors formed a joint venture with GAC Component Co. Ltd.(GACC, Guangzhou, China) to begin production of thermoplastic composite (TPC) liftgates for a global automaker’s crossover vehicle starting in late 2018.
- Kangde Group (Hong Kong) entered an agreement with BAIC Motor to build an Industry 4.0 smart factory in Changzhou to produce CFRP car body and other components beginning in 2019 and scaling to 6 million parts/yr — its 66,000 MT/yr carbon fiber facility in Rongcheng will begin production in 2023;
- HRC (Shanghai, China) commissioned the first Rapid Multi-injection Compression Process (RMCP) automated composites production line from Carbures (El Puerto de Santa María, Spain); and
- Volvo’s new, separately branded electric high-performance car company Polestar started production of its first model, Polestar 1, in 2019 in the new Polestar Production Centre in Chengdu.
- The industry’s first carbon fiber composite pickup box was unveiled in 2018 by General Motors (GM, Detoit, Mich., U.S.). The first-ever composite bed for a full-size truck was actually built by GM in 2001, but the take-up rate on the Silverado and Sierra Pro-Tec box option was only 10% of what GM expected. Thus, it waited more than 15 years to try again. The CarbonPro pickup box, again an option, but for the 2019 GMC Sierra, was developed with Teijin Automotive(Tokyo, Japan), which acquired Continental Structural Plastics (CSP, Auburn Hills, Mich., U.S.) in 2017. CSP has years of experience manufacturing composite boxes for the Honda Ridgeline and Toyota Tacoma trucks, both made from chopped glass fiber sheet molding compound (SMC). The first-generation Honda bed was 30% lighter than steel when it debuted in 2005, but its 2017 update switched away from SMC in two of the components, opting for a direct long-fiber thermoplastic (D-LFT) for the sidewalls and headboard and for a short-fiber compound for the spare tire tray, both injection molded using glass fiber and polypropylene (PP). The 2019 GMC CarbonPro box also uses Teijin’s Sereebo thermoplastic composites manufacturing process, which combines a mat of 20-millimeter-long carbon fibers with nylon 6 that is compression molded for part cycle times of 60–80 seconds.
- This growing trend toward use of thermoplastics in automotive composites is aided by processes such as overmolding, where blanks made of woven or unidirectional fibers in a thermoplastic matrix — known as organosheet — are compression molded into a 3D shape while reinforced plastic is injection molded on top and around to form complex-geometry ribs, bosses, inserts and attachment points. Parts in development or production include seat backs, seat rests, airbag housings, A and B pillars, door cross beams, bumper beams and large floor components. Although overmolding is typically all-thermoplastic, the Opto-Light project, managed by Aachen Center for Integrative Light Construction (AZL) at RWTH Aachen University (Aachen, Germany), demonstrated thermoplastic overmolding onto a thermoset carbon fiber/epoxy shell to produce a 3D structural portion of the BMW i3 floor panel in a fully automated cell with a 2-minute cycle time. The project also showed the ability to use cure-state monitoring via Netzsch Gerätebau (Selb, Germany) in-mold sensors to achieve thermoplastic-to-thermoset joining without laser ablation as an intermediate step. This second advance stops compression molding of the high-performance, low-creep thermoset shell at the optimized time to leave sufficient reactivity in the epoxy resin to achieve covalent bonding, hydrogen bonds and/or semi-interpenetrating networks with the overmolded PA 6 thermoplastic.
- Notably, the Opto-Light demonstration part started with unidirectional (UD) tape. This trend to use UD tapes to reduce waste compared to woven or noncrimp fabric (NCF) reinforcements continues to grow. Because the tapes can be cut and placed precisely, very little scrap is produced and fibers can be aligned more precisely to match loads. One notable example is the CFRP rear wall for the Audi A8 luxury sedan made in a fully automated, Industry 4.0 production line by Voith Composites (Garching, Germany). It provides 50% weight reduction compared to three to five welded aluminum parts, and 33% of the drive cell’s torsional stiffness. The rear wall begins with Zoltek (St, Louis, Mo., U.S.) 35K carbon fiber which is spread into bindered, 50-millimeter-wide, UD tape, which is cut and laid at specified angles to form a tailored blank in a single machine — the Voith Roving Applicator. This blank is shaped into a 3D preform in a heated press supplied by FILL (Gurten, Austria) which adapts the pressure applied as it stamp-forms separate regions of the preform clamped in the forming tool made by ALPEX Technologies (Mils bei Hall, Austria). The completed preform is then injected with resin and press-molded using the Audi-developed Ultra-RTM process, which uses less than 15 bar of pressure compared to 140 bar common for high-pressure RTM (HP-RTM). Thus, only 350 kilonewtons of press force is needed compared to 2,500 for HP-RTM. Although the VORAFORCE 5300 epoxy resin cures in 90–120 seconds at 120°C, the total part cycle time is 5 minutes.
- Another alternative to HP-RTM is wet compression molding (a.k.a., liquid compression molding), which does use snap-cure resins and NCF, but also lower pressure. Instead of injecting resin into the preform, automated equipment spreads resin over the fabric and then transfers this into a thermoforming press. Eliminating the preforming step and offering cycle times less than 90 seconds and less-expensive equipment, BMW has predicted a significant increase in wet-pressed parts. Huntsman Advanced Materials (Basel, Switzerland) has developed a next-generation process called dynamic fluid compression molding (DFCM) that claims fiber volumes up to 65% and the ability to mold more complex geometries.
- For exteriors, ultra-lightweight SMC continues its push below 1.0 g/cc and carbon fiber is also gaining ground, with Polynt Composites (Scanzorosciate, Italy), Aliancys (Schaffhausen, Switzerland) and CSP all adding new SMC production lines over the past few years, all of which have the ability to make carbon fiber SMC. Polynt has also introduced Polynt-RECarbon recycled fiber SMC to its product offerings, as well as UDCarbon and TXTCarbon compounds featuring unidirectional and fabric reinforcements, respectively. The potential for these products can be seen in the front subframe development project completed by Magna International (Aurora, Ontario, Canada) and Ford Motor Co. (Dearborn, Mich., U.S.), which uses locally reinforced and co-molded chopped carbon fiber SMC with patches of SMC made with carbon fiber 0-degree/90-degree NCF. This SMC structural subframe must handle significant loads, supporting the engine and chassis components, including the steering gear and the lower control arms that hold the wheels. Though only a development part, it achieved an 82% parts reduction, replacing 54 stamped steel parts with two compression molded composite components and six overmolded stainless steel inserts, while cutting weight by 34%.
- Hybridizing SMC with prepreg is an approach used by Ford’s global Research and Advanced Engineering group teamed with its Chassis Engineering group in the U.K. to redesign a production steel suspension knuckle for a C-class vehicle. By co-molding layers of woven carbon fabric prepreg with chopped carbon fiber SMC, a complex-shaped, high-performance suspension knuckle was produced with a cycle time of less than five minutes and a 50% weight reduction. Other developments include Saint Jean Industries (Saint Jean D’Ardières, France) and Hexcel (Stamford, Conn., U.S.) developing a hybrid carbon fiber/aluminum version of a performance car suspension knuckle, which increased stiffness by 26% compared to an all-aluminum knuckle. Meanwhile, Williams Advanced Engineering (Grove, Oxfordshire, U.K.) has developed a CFRP wishbone that uses unidirectional carbon fiber and recycled carbon fiber nonwoven mat — up to 80% of the composite part, by weight — to cut weight 40% compared to conventional aluminum versions, yet its cost is comparable to aluminum forgings. The part molded is in 90 seconds using an HP-RTM process called RACETRAK for a 5-minute total cycle time, including layup.
- Pultrusion is another growing trend. In 2018, L&L Products launched its Continuous Composite Systems (CCS) pultrusions using polyurethane resin and glass, carbon or hybrid fiber reinforcement for automotive applications such as side sills and crash structures. Designed to replace traditional metal structures that require bulkheads for necessary stiffness, CCS pultrusions offer light weight — 75% less mass than steel and 30% less than aluminum — at an economic price. In 2019, the automotive industry’s first curved, multi-hollow pultruded carbon fiber bumper beam was unveiled in the 2020 Chevrolet Corvette Stingray. In development since 2016, the part is produced by Shape Corp. (Grand Haven, Mich., U.S.) using Scott Bader (Northamptonshire, U.K.) Crestapol urethane acrylate resin and Thomas Technik & Innovation’s (TTI, Bremervoerde, Germany) Radius-Pultrusion system. Pultrusion is again front and center in the MAI Skelett project, which thermoformed and overmolded UD carbon fiber thermoplastic pultrusions in a two-step, 75-second process to produce a demonstrator BMW i3 structural roof member. The part exceeds all previous version requirements, integrates clips for attachments and changes crash behavior from brittle to ductile failure mode for increased body-in-white (BIW) residual strength.
- One final trend is the move toward hybrid metal-composite structures. The System integrated Multi-Material Lightweight Design for E-mobility (SMiLE) consortium combined composites and non-ferrous metals to reduce mass and costs for the entire BIW structure of a battery-electric vehicle. The rear load floor module uses eight layers of 60-wt% UD glass fiber-reinforced PA6 Ultratape and 40-wt% glass fiber/PA6 Ultramid direct-long-fiber thermoplastic (D-LFT), both from BASF SE (Ludwigshafen, Germany). SMiLE developed a new process, taking a preconsolidated tape laminate and selectively reinforcing that with D-LFT where ribs and complex geometries are needed. This is then placed, along with two aluminum profiles and several metallic inserts, into a compression molding press and quickly cycled to form a 1.3-by-1.3-meter part. This rear module is adhesively and mechanically joined to a second, hybrid/thermoset composite forward load floor, made using RTM and carbon fiber-reinforced epoxy with integrated metallic inserts and local sandwich structures containing polyurethane-foam cores.
- In the FlexHyJoin project, managed by the Institut für Verbundwerkstoffe (IVW, Kaiserslautern, Germany), an automated process enabling a thermoplastic composite roof structure to be assembled into a metal BIW was achieved by laser pretreating metal brackets and attaching these to the composite roof bow via induction and laser joining. This was achieved in a single, automated production cell with integrated process control and inline nondestructive testing (NDT) with a cycle time of 140 seconds.
Boatbuilding and marine
- Boatbuilding and marine: Hinckley Yachts’ Dasher features carbon fiber/epoxy construction and electric propulsion. Source | Hinckley Yachts
The National Marine Manufacturers Assn. (NMMA, Chicago, Ill., U.S.) reported in 2019 that unit sales of new powerboats increased 4% in 2018, reaching 280,000, the highest total since 2007 for the U.S. recreational boating industry. NMMA predicts 3–4% growth for 2019 and noted that boat manufacturers have concentrated on new products, especially in fishing, watersports and pontoon boats. NMMA’s top trends for 2018 included:
- Wakesport boats represented the recreational boating industry’s highest growth in 2018 (9–11%), totaling 10,000 units.
- Pontoon boats increased 4–6%, to 58,000 units, valued for their versatility in use for fishing to cruising to watersports.
- Personal watercraft continued to stay strong, with an entry-level price, growing by 6–8% to 68,000 units.
The trends for larger production boats powered by outboard engines (compared to inboard diesel engines), as well as increasing use of carbon fiber (CF), epoxy resin and 3D printing continue. In the Jan. 2019 forecast by Boating Industry, Ryan Kloppe, director of sales at Statistical Surveys Inc., said his company was expanding its 16- to 40-foot reporting category to 45 feet. “People are building bigger boats,” he said, noting continued growth in larger boats powered by outboards for fishing and cruising.
- Examples of outboard-powered boats — more than 40 feet long, each with at least three or four engines clamped to the transom — include Scout Boats’ (Summerville, S.C., U.S.) 530 LXF (53 feet), HCB Yachts’ (Vonore, Tenn., U.S.) 53-foot Sueños and 65-foot Estrella center consoles, and Midnight Express’ (Miami, Fla., U.S.) 60-foot Pied-A-Mer. Outboards are chosen for their light weight and reduced requirement for systems and space inside the hull. As with cars, space in boats is at a premium.
- The increasing size and number of outboards per boat is driving the need for reduced weight in composite hulls and decks, but without sacrificing performance. The latter means not only long-term durability in the water but higher speeds and resistance to wave-slamming loads, as well as heat resistance beneath dark paint colors, which continue to be popular. Carbon fiber and epoxy provide a particularly effective combination, and, in fact, are used on Scout’s 530 LXF and 420 LXF models, manufactured via resin infusion. Carbon fiber is also used in HCB’s Estrella. Hinckley Yachts (Southwest Harbor, Maine, U.S.), renowned luxury production builder and longtime veteran of resin infusion, has begun switching all of its sailing and power models to epoxy, while its 40-foot Sport Boat models and Dasher fully electric motor yacht feature CF/epoxy construction. Note, however, that these brands represent the high end of the market. Boats priced in the middle of the market typically use glass fiber and vinyl ester resin, though resin infusion has become much more common. Polyester resin is still used for the lowest-priced boats. Carbon fiber is creeping into medium-priced boats, used to cap hull stringers and in accessories like hard tops where owners are willing to pay for higher-priced options.
- Price, however, is an issue, as explained by an Ohio respondent to Boating Industry’s survey: “The industry has priced product out of reach for the middle-class boater. The guy who bought the ‘starter’ boat and allowed boat builders and motor companies to grow has been removed from the market. We need to target a younger crowd with [affordable] price point boating products.”
- One boat trend that might appeal to a younger market is electrification. “As hybrid gas/electric cars such as Tesla and Prius have grown in popularity and become more practical options for mainstream consumers, boat manufacturers have begun to follow suit,” explains a 2019 guide for buyers on Boattrader.com. Though electric-drive boats have been heralded as “the future” for some time, and were actually the norm for powerboats before the 1930s, their advance into today’s market has been slow. However, with battery and hybrid power technologies dropping in cost thanks to the auto industry’s continued development, sailboats and small cruising power boats are being introduced that eliminate the tanks, fumes and environmental impact of fossil fuels. Examples include Hinckley’s Dasher, the 12-meter long, 16-passenger Soel Cat 12 by Soel Yachts (Delft, Netherlands), the 7.47-meter 740 Mirage Air center console by Frauscher (Gmunden, Austria), Q Yachts’ (Finland) Q30 tender and the Secret 33 water taxi, ElectraCraft’s (Westlake Village, Calif., U.S.) electric pontoon boats and Greenline Yachts’ (Begunje, Slovenia) line-up of electric and hybrid models 10 to 21 meters long. This trend is expected to gain more momentum as reliable cruising range and speed are established (note the new electric boat speed record of 88.6 mph set in July 2019). Most docks already have electrical power for recharging.
- A project reiterating this point is the all-composite hydrofoiling watercraft developed by SeaBubbles (Paris, France) with support from composites fabricator Décision SA (Ecublens, Switzerland) and Sicomin Epoxy Systems (Chateauneuf les Martigues, France). This eco-conscious taxi transport solution for the world’s urban waterways is based on a hydrofoil design that allows the watercraft to glide silently above the water when it exceeds 12 kilometers per hour, which reduces drag 30–40%. A clean-charging electric drive system converts solar, wind and water power so the vessel does not generate any CO2emissions. SeaBubbles began testing the craft on the River Seine in Paris in September 2019; if all goes well, commercial service could begin in Paris in 2020. The technology’s makers hope to spread SeaBubbles to more than 50 waterway-rich cities worldwide.
- Another trend is the growing use of 3D printing in marine. Already, high-end yachts are using 3D-printed parts. For example, Hinckley’s Dasher electric features a stylish console supported by six parts that nest and interlock, 3D printed in partnership with the University of Maine’s Advanced Structures & Composites Center (UMaine, Orono, Maine, U.S.). According to Hinckley’s director of engineering Scott Bryant, the tight-tolerance pieces would have been difficult to produce with traditional molded fiberglass reinforced plastic (FRP) due to resin shrinkage. Now, the UMaine Composites Center boasts the world’s largest prototype polymer 3D printer, largest solid 3D-printed object and largest 3D-printed boat. The 3D printer, called MasterPrint and produced by Ingersoll Machine Tools (Rockford, Ill., U.S.) in partnership with Oak Ridge National Laboratory (Oak Ridge, Tenn., U.S.), can print objects as long as 100 feet by 22 feet wide by 10 feet high, depositing 500 pounds of material per hour. UMaine’s claim on the largest 3D-printed boat is its 25-foot, 5,000-pound 3Dirigo, being tested in the Alfond W2 Ocean Engineering Laboratory, an offshore model testing facility with wave basin.
- The world’s first 3D-printed boat was a 6.5-meter-long and 3-meter-wide Mini 650 sailing yacht, designed by Livrea Yachts (Palermo, Italy) and built by sister company Ocore in partnership with Autodesk (San Rafael, CA, US), Lehvoss Group (Hamburg, Germany) and Kuka Robotics (Augsburg, Germany). Ocore is using fused deposition modeling (FDM) via a mounted extrusion head on a 2.5-meter-tall Kuka robot. The head melts compounded 25% chopped carbon fiber-reinforced polyamide (PA, or nylon) pellets and deposits 0.6-millimeter-thick layers to form the hull, rudders and other components. The hull is printed in sections called isogrids, which resemble an aerospace skin-stringer design, with a CFRP corrugation between two CFRP skins. The isogrids are joined with structural adhesive and sheathed with skins of carbon fabric. Advantages claimed include a hull built in just days, enabling the team to print different hulls, analyze the speed forecast and identify the optimal shape.
- While printing boat structures is just at its beginning, the move toward 3D-printed molds is continuing to gain momentum. Projects completed include a boat hull pattern by Marine Concepts (Cape Coral, Fla., U.S.) and a 10.4-meter-long hull construction mold by Xplora Yachts (Kirkland, Wash., U.S.). The Marine Concepts pattern was a collaborative proof-of-concept project with Thermwood Corp. (Dale, Ind., U.S.) and custom compounder Techmer PM (Clinton, Tenn., U.S.). The pattern was 3D-printed slightly oversized, over roughly 30 hours, and subsequently trimmed to final size and shape, using Thermwood’s trademarked Large-Scale Additive Manufacturing (LSAM) system. The printed material was Techmer’s trademarked Electra l ABS LT1 3DP. The final tool was printed in six sections, four major center sections with walls approximately 38 millimeters thick and a solid printed transom and bow. Sections were pinned and bonded together using a Lord Corp. (Cary, N.C., U.S.) multicomponent urethane adhesive. The assembled pattern was then machined as a single piece on the same Thermwood system in about 50 hours. The entire print, assembly and trim process reportedly required fewer than 10 working days. The pattern was subsequently used to pull a fully functional production hull mold made with conventional fiberglass reinforced plastic (FRP) molding methods.
- The Xplora Yachts hull construction mold was 3D-printed start to finish, in partnership with Oak Ridge National Laboratory (ORNL, Oak Ridge, Tenn., U.S.) using its Big Area Additive Manufacturing (BAAM) machine, manufactured by Cincinnati Inc. (Harrison, Ohio, U.s.). Although three mold sections could be printed simultaneously in 12 hours, all 12 sections of the mold were printed over a five-day period, using 2,495 kilograms of 20% chopped carbon fiber/ABS Electrafil J-1200 from Techmer PM at $11/kilogram for a total material cost of $27,500. The sections were printed with an extra 3.8 millimeters of material which was later machined to a smooth surface. Rods were assembled cross- and length-wise to build the sections with Ashland’s (Dublin, Ohio, U.S.) Pliogrip Plastic Repair 10 epoxy applied to the seams. Designed for ABS, the epoxy adhesive’s 60-minute cure time allowed alignment adjustments during assembly. Assembly was completed in three hours and the adhesive cured within 24 hours. A Faro (Lake Mary, Fla., U.S.) laser-tracking system was used to compare the mold surface to original CAD data and showed an average deviation of less than 1.27 millimeters. After being sanded and coated with tooling gelcoat and mold release, the mold was used to resin infuse a prototype E-glass and Kevlar foam-cored hull.
- Future molds may be printed in thermoset composites, however, using the new Reactive Additive Manufacturing (RAM) machine, developed by Magnum Venus Products (MVP, Knoxville, Tenn., U.S.) in collaboration with Polynt Composites (Carpentersville, Ill., U.S.) and ORNL. Unveiled in Sept. 2019 as the world’s first large-scale thermoset composite additive manufacturing system, the RAM prints in a build envelope of 8 feet by 16 feet by 3.5 feet using Polynt Reactive Deposition PRD-1520 print media that cures at ambient temperature without UV activation. This technology is aimed at low-cost fixtures, thermoforming tools and autoclave molds, as well as a wider range of applications that require higher thermal properties afforded by thermoset polymers.
- The RAM system includes the large print platform and a floor-mounted MVP pumping system, with only the printhead mounted onto the computer-controlled gantry. The pumping system accurately measures and meters the short glass fiber-reinforced vinyl ester resin and peroxide initiator into a static mixer in the printhead. The mixed resin is then extruded through a nozzle, similar to most fused deposition modeling (FDM) systems. Print speed is roughly 1.2 m/s using a 1.2-millimeter diameter nozzle. RAM reportedly can achieve FDM-scale features while still delivering a high output of almost 7 kg/hr (15 lb/hr).
Civil infrastructure
- Civil infrastructure: Composite Advantage’s (Dayton, Ohio, U.S.) fiber-reinforced polymer (FRP) FiberSPAN system was recently used by the Nevada Department of Transportation (NDOT) to build a shared-use path along Nevada’s State Route 88. Source | Composite Advantage
- Composites offer light weight, corrosion resistance, high strength and long lifespan — qualities that make them a natural fit for infrastructure projects. And while composites are already being used to rehabilitate roads, bridges, water/drainage systems and seawalls, and to build resilient structures, widespread adoption has yet to occur.
- However, the role of composites in infrastructure is at an interesting point. In August 2018, bipartisan legislation was introduced in the U.S. aimed at encouraging research and use of innovative materials for infrastructure projects. Known as the Innovative Materials for America’s Growth and Infrastructure Newly Expanded (IMAGINE) Act, the bill seeks to lead decision-makers involved in construction and infrastructure projects to consider innovative materials as an option. The idea behind the legislation is that education about the benefits and properties composites will help designers and engineers rethink infrastructure projects.
- Aging infrastructure continues to offer a potentially huge market for composite materials. According to a 2019 report from the American Road and Transportation Builders Association, more than 47,000 bridges of the more than 600,000 bridges in the U.S. are in poor condition and in need of urgent repairs.
- Decaying bridges are just one of the infrastructure concerns that have encouraged the development of a number of composites-enabled technologies. The early deterioration of concrete due to the corrosion and failure of steel rebar has been well documented. Conventional repairs could cost billions. In many locales, the useful life of corrosion-prone steel-rebar-reinforced concrete is limited to 25 years, rather than the 75–100 years once promised by its advocates. Therefore, the lifecycle cost advantages, not to mention the safety benefits, of using composite rebar continue to overcome resistance among change-averse municipalities.
- Progress is being made. The critical need for bridge designs that can resist corrosion and extend useful life are a big part of growing awareness of the role composites — particularly fiber-reinforced polymer (FRP) — can play in rehabilitating crumbling infrastructure. Projects such as pedestrian bridges are slowly helping to build the case.
- For example, Composite Advantage’s (Dayton, Ohio, U.S.) FRP FiberSPAN system was used by the Nevada Department of Transportation (NDOT) to build a shared-use path along Nevada’s State Route 28. The NDOT and the Tahoe Transportation District opened the new Tahoe East Shore Trail in June 2019. Traveled by more than 1 million visitors every year, State Route 28 is a two-lane, mountainside road bordering 11 miles of Lake Tahoe’s undeveloped shoreline. NDOT initiated a shared-use path project to support expectations of doubled traffic over the next 20 years, while protecting the area’s ecosystem and dealing with problems of limited parking at the site and lack of safe access points. Composite Advantage’s FiberSPAN was chosen to meet the demands of constructing a shared-use path on the region’s uneven slopes. Thirty-two 40-foot bridge span sections were installed on an 11-mile section of the path. The spans were grouped to create five distinct bridges, used in areas where the slope was too steep to provide flat walking surfaces. The FRP decks are 134 inches wide and have a 5-inch structural thickness at the thinnest section, with a 1% cross slope. The panels were coated with a 1/8-inch non-slip polymer aggregate surface, and weigh 8.8 psf. The deck weight, including wear surface, curbs and railing, is 12 psf. Specification requirements called for a uniform live load of 90 psf pedestrian loading. Mid-span deflection of the deck is limited to L/500 and the mid-span deflection of the superstructure is limited to L/360. Vehicle maximum loading is rated at H-5 for a rear axle load of 8,000 pounds. Mid-span FRP deflection is limited to L/300, and uplift load is rated at 30 psf.
- In addition to the bridge decks, Composite Advantage’s offerings include composite pilings and fender systems, which have been used to rehabilitate aging waterfront infrastructure including bridges at a seaside resort at the southern tip of New Jersey’s Cape May Peninsula and the Jamestown-Scotland Ferry Terminal in Virginia.
- In other parts of the world, composites use in replacing civil infrastructure continues to advance. In 2019, FiberCore Europe partnered with Sustainable Infrastructure Systems to produce composite bridges in Australia. FiberCore Europe’s InfraCore Inside technology enables composite structures that meet all standards and government requirements while providing a practically maintenance-free service life of 100 years. More than 900 bridges and lock gates — from bicycle and pedestrian bridges to the world’s longest bridge span in composites — have been installed in the Netherlands, Belgium, England, France, Italy, Sweden, Norway, China, the U.S. and now in Australia.
- Technologies such as additive manufacturing are beginning to play a larger role in infrastructure projects as well. For example, Royal HaskoningDHV (Amersfoort, Netherlands), CEAD (Delft, Netherlands) and DSM (Amsterdam, Netherlands) have designed a lightweight, 3D-printed, fiber-reinforced polymer (FRP) pedestrian bridge prototype. The bridge consists of a glass fiber-filled thermoplastic PET (DSM’s Arnite) reinforced with continuous glass fibers during the 3D printing process. This combination is said to offer high strength, versatility and sustainability.
Construction
- Construction: Core Composites has developed its all-composite, fast-build Joint Warfighter Shelter of the Future. Source | Core Composites
- In the 21st century, one of the more compelling human stories is the growing need for resources to house Earth’s expanding population, and the growing awareness that those resources are finite and, in many cases, increasingly scarce. One case in which that contrast is acute is residential housing. The United Nations foresees a deepening global housing crisis — more than 440 million urban households will be in need of affordable accommodation by 2025. But conservationists warn that the sustainability of Earth’s forests, the source of the lumber to build those accommodations, is at serious risk. This conflict has done much to pique interest in fast-build construction technologies based on fiber-reinforced composites. As the new century’s third decade begins, composite manufacturers’ efforts in the housing arena are picking up speed.
- An example of composites use in a fast-build application is an all-composite military shelter developed by Core Composites (Bristol, R.I., U.S.). The Joint Warfighter Shelter of the Future (JWSOF) is funded by the U.S. Army Medical Command (San Antonio, Texas, U.S.) and is a next-generation surgical, rigid wall shelter with an exterior of a 20-foot ISO shipping container that expands via a series of lightweight composite expanding walls, roofs and floors. Core says the shelter is stiffer, stronger, 41% larger and 25% lighter compared to legacy aluminum shelters. The composite system comprises carbon fiber fabric, fire retardant resin, PET foam core and a multi-side infusion manufacturing process. Core Composites used A&P Technology’s (Cincinnati, Ohio, U.S.) QISO carbon fabric for the project.
- Use of composites in marine pier structures is also growing. An example of this is the Manahawkin Bay Bridge that links mainland New Jersey (U.S.) to Long Beach Island. New Jersey Department of Transportation (NJDOT) authorities wanted to surround the bridge’s deepest structural piers with energy-absorbing structures that would prevent damage to them from a large, out-of-control vessel. In this case, NJDOT specified an impact load or force of 40.76 kip-ft, which it calculated would be produced by a 200-ton hopper barge, the largest vessel that NJDOT knew would ply the waters beneath the bridge, says House. The Manahawkin piles would be fendering piles, which would need to resist lateral loads. The hollow tubes would be driven down into the sea bed far enough so that the soil friction provides fixity, to hold them in place. These tubes would then be filled with concrete.
- To make the piles, heavy quadraxial fabrics supplied by Vectorply Corp. (Phenix City, Ala., U.S.) are combined with polyester or vinyl ester resin, supplied by Polynt Composites (Carpentersville, Ill., U.S.) or other suppliers, in a proprietary manufacturing process that combines vacuum infusion with centrifugal casting. The closed mold is spun to help compact the fibers during the infusion process. The quadraxial fabrics ensure that at least 50% of the fibers run axially along the pile length, and about 25% of the fibers end up as hoop direction reinforcement. The remainder are oriented at 45 degrees. All piles are gel coated, with product supplied by Polynt Composites or INEOS Composites (Columbus, Ohio, U.S.) for added durability and appearance.
- On the horizon, keep an eye out for the Lucas Museum of Narrative Art, currently under construction in Los Angeles’ Exposition Park near the Unviversity of Southern California. The museum, founded by filmaker George Lucas and his wife, Mellody Hobson, Co-CEO and President of Ariel Investments, was designed by architect Ma Yansong and features a highly organic and unusually shaped design that will feature new public green space, state-of-the-art cinematic theaters, a research library, numerous spaces for onsite education, restaurants, retail and event spaces. It will also feature significant use of composite materials.
Industrial applications
- Industrial applications: Hudson Product’s Wickert press, used to mold the Tuf-Lite IV fan blade.
- Although the use of composites in high-performance end markets like aerospace and automotive often receive most of the industry’s attention, the fact is that most of the composite materials consumed are applied to non-high-performance parts. The industrial end market falls into that category, and here material performance often emphasizes corrosion resistance and durability, particularly in applications involving the storage of chemicals and gases.
- Indeed, composite storage tanks are proving increasingly valuable in several geographic regions. In South America, Tecniplas (Sao Paulo, Brazil) has developed a strong reputation for the fabrication of large composite storage tanks that contain everything from water to fertilizers to industrial solvents. In the U.S., Ershigs (Bellingham, Wash., U.S.) has established its own niche as a supplier of composite tanks, piping, ducts and scrubbers.
- Emblematic of the type of work being done in industrial composites is Hudson Products (Hudson, Beasley, Texas, U.S.), a manufacturer of air-cooled heat exchangers and axial flow fans. The company’s fiberglass Tuf-Lite axial flow fans have been in production for more than 60 years, with more than 250,000 in use globally. The Tuf-Lite fan series got its start in 1955 with the Tuf-Lite I, featuring a glass fiber-reinforced composite blade. Since its creation, the fan has gone through a few iterations. Tuf-Lite II was introduced in 1984 to increase the manufacturability of the fan’s parts, followed in 2004 by Tuf-Lite III. Tuf-Lite II and Tuf-Lite III fan designs use a proprietary vinyl ester resin in a resin transfer molding (RTM) manufacturing process. For the newest version, the Tuf-Lite IV, the company employed computational fluid dynamics (CFD) technology for a design that focused on noise reduction and efficient airflow. Tuf-Lite IV is also 20% larger. Hudson turned to Wickert Hydraulic Presses (Hebron, Ky., U.S.; Landau, Germany) for a new custom press, which enables changes to the layup sequence, type of fiberglass, material configuration, number of layers, resin injection points and positioning of vent lines. The result is a more efficient, more effective fan blade.
- One of the more unusual recent industrial applications of composites was a rail bogie, the four- or six-wheel trucks that support rail vehicles and provide traction and braking. The prototype bogie, developed in the U.K., is made primarily with recycled carbon fiber composites but is supplemented with virgin carbon fiber composites in places that require additional strength or stiffness. The bogie was developed by ELG Carbon Fibre Ltd. (Coseley, Dudley, U.K.), which supplies the recycled carbon fiber and performed much of the materials testing; Magma Structures (Portsmouth, U.K.), designer and fabricator of the rail bogie; the University of Birmingham (Birmingham, U.K.) Sensors and Composites Group, which worked with Magma to develop an embedded health monitoring system for the bogie; and the University of Huddersfield (Huddersfield, U.K.), on whose dynamic test rig the prototype is to undergo initial full-scale testing. Alstom U.K. (London) helped to assemble the consortium and has provided additional support through consulting and existing bogie design information. The consortium selected ELG’s Carbiso M, a nonwoven mat made with standard modulus fiber (strength of 4 to 5 GPa) in an epoxy matrix. They demonstrated that the fatigue performance of the recycled carbon fiber/epoxy is similar to that of conventional woven carbon fiber laminates — and better than that of structural steel. Finite element analysis (FEA) performed by Applied FEA Ltd. (Southampton, U.K.) verified fatigue service loads as well as exceptional static loads. The prototype is 36% lighter than the steel alternative; the composite frame itself yields a 64% weight savings, but the prototype suffers a weight penalty from paint and the tapping plates needed to attach the steel fittings. Considering the frame alone, the 590 kilograms of weight saved is estimated to produce an annual savings in operating costs of between £8,000 and £62,000, depending on the train’s service type and mileage. Additionally, each bogie frame could reduce CO2 emissions through its lifetime by as much as 68 metric tonnes.
- Also emerging is the increased use of composites in tanks used to store cryogenic liquids. Along these lines, Cimarron Composites (Huntsville, AL, US) announced in 2018 that it had made a leap forward in all-composite cryogenic tank development, achieving 15,000 micro-strain performance with a carbon fiber-reinforced composite tank in a pressurized liquid nitrogen environment. Successful operation at such a high strain level allows the liner-less composite tank structure, made with a mixture of textiles and continuous wound fibers, to be much thinner than what was previously needed in these types of tanks, without the cost and mass of the liner. According to Cimarron, earlier composite tank programs were limited to 3,000 micro-strain due to materials and processing limitations, and this resulted in extra mass. Cimarron’s new tank technology uses a material system that performs well at extremely low temperatures without developing the microcracks that create leak paths for fluids like liquid oxygen, liquid hydrogen or liquid methane.
Electronics
- Electronics: SABIC demonstrated in a recent study that a 1-millimeter-thick cover could meet all relevant industry performance specifications for very thin notebook computers or tablets.
- The consumer electronics market is one of constant change. Products such as smartphones, smartwatches, tablets and laptops evolve quickly. OEMs scramble to keep up with consumer demands: faster operating speeds, more features, longer-lasting batteries.
- When it comes to covers, cases and frames for such products, OEMs are seeking materials with strong aesthetics and design freedom, good impact resistance and high stiffness at low weight with thin wall sections. There is also a need for cost-effective, high-volume processing methods that can meet global production demand in the tens of millions of units annually.
- A feasibility study conducted by SABIC (Bergen op Zoom, Netherlands) involved use of two types of thermoplastic composites to produce a 1-millimeter-thick notebook-computer/tablet cover. The study showed the hybrid thermoplastic composite design could be a viable solution for the challenging consumer electronics market.
- Covestro’s (Leverkusen, Germany; Shanghai, China) Maezio brand of continuous fiber-reinforced thermoplastic (CFRTP) composites, which launched in October 2018, is also attracting interest in the electronics industry. The product line includes unidirectional (UD) reinforced tapes and sheets made from carbon fibers impregnated within a polycarbonate (PC) matrix. According to Covestro, the CFRTP can be tuned for performance, aesthetics and economies of scale, and can be used in products in a range of industries. Maezio can be thermoformed at high yield rates and shorter cycle times, and is said to reduce costs for millions of parts per year. Other production technologies such as overmolding, automated tape laying (ATL) and automated fiber placement (AFP) can also be integrated. The main advantage of Maezio is its tuneability. The UD tapes, which are just 120 microns thick, can be laminated at different angles to form sheets tuned to meet a variety of performance and mechanical criteria. Resulting sheets are strong, stiff, lightweight and have a natural, unidirectional surface finish. In addition, CFRTP composites are recyclable.
- While covers and cases get a lot of attention, composites also play a substantial role in interior electronics components. For example, Samsung’s (Seoul, South Korea) Galaxy Note9, which launched in 2018, employs a Water Carbon Cooling system that is said to allow the phone to run more smoothly during heavy use. According to Samsung, the cooling system consists of a heat pipe, or “thermal spreader,” that water phase changes to efficiently dissipate heat. First, a porous structure filled with water absorbs the heat, then the water is turned into steam and moved through pipes. As the steam begins to cool and turns back into water, the process begins again. The Galaxy Note9 has a larger heat pipe than its prede cessor and also benefits from an enhanced carbon fiber TIM (thermal interface material) that is said to transfer heat from the processor to the thermal spreader with 3.5 times greater efficiency, boosting thermal conductivity and helping to prevent overheating.
- In addition, glass fiber/epoxy laminates have been the foundational structural substrate in printed circuit boards (PCBs) for decades. These iconic thin, green “cards” support the transistors, resistors and integrated circuits at the heart of almost all digital technologies, and connect them electrically via conductive pathways etched or printed on their surfaces. Multilayer PCBs are made by interleaving copper clad (and etched) laminates with high resin content (HRC) prepreg layers and then compressing into an integrated structure. Holes are then drilled and plated with copper to create vias connecting the etched circuits within. The cores serve as the structural units while the HRC prepreg provides dielectric insulation between adjacent layers of copper circuits.
- According to industry sources, the global PCB market is expected to reach an estimated $80.1 billion by 2023, with a CAGR of 3.3% from 2018 to 2023. Market growth factors for the PCB market include increased adoption of automation in various end-user industries, increased demand for wireless devices, increasing miniaturization of devices, the need for increased efficiency of interconnected solutions and increased demand for flexible circuits.
- Glass fiber/epoxy’s dominance in the electronics market has been under challenge as many of these trends — notably, miniaturization, better thermal management, increased speed and performance, and 3D printing — force PCB manufacturers to re-examine their material options.
Fuel cells and batteries
- Fuel cells and batteries: Williams FW-EVX features CFRP battery module boxes made with the 223 fold-to-form process.
- More than 80 concept, demonstrator and/or test-fleet fuel-cell-powered electric vehicles have been fielded by 25 automakers worldwide since General Motors (Detroit, Mich., U.S.) unveiled the first, its GM Electrovan, in 1966. The most recent to the market is the Toyota Mirai. There have also been a host of fuel-cell-powered trucks, buses, racing vehicles, a motorcycle, four rail locomotives and some ocean vessels, including submarines. Fuel cells also power an increasing number of stationary systems that provide heat and light to other structures. According to global analyst IHS Markit (London, U.K.), use of battery-electric vehicles (BEVs) is expected to expand to as many as 90% of all vehicles in western countries by 2025, but hydrogen fuel cell vehicles (HFCVs) may quickly become a more aggressive competitor as new technologies develop. Eleven large corporations have formed the Japan H2 Mobility cooperative and the German counterpart H2 Mobility Germany, and both have targets to increase H2 fueling stations, up from 100 and 69 currently. Though California lags in stations (36), it boasts the most HCVs on the road at 4,410. Multi-client studies by IHS Markit forecast a significant share of hydrogen in the mobility sector by 2050, led by global truck and car manufacturers like Toyota, Nikola Motors, Hyundai and Bosch. IHS Markit suggests that in order for this growth to take place, hydrogen prices will first need to come down from current levels.
- There are also opportunities in non-transportation sectors including decarbonizing energy use for industry and local electrical power. The U.K. is exploring the possibility of converting its natural gas grid to H2 with its ongoing North of England H21 project, due to begin in 2028. Residential and commercial heating and cooling accounts for about 40% of final energy demand in Europe.
- Composites can make up the bipolar plates, end plates, fuel tanks and other system components of proton exchange membrane fuel-cell (PEMFC) systems, still the leading type. In the past, thermoset materials were thought to be limited to lower volume and stationary applications, due to their longer mold cycle times, higher scrap rates and an inability to produce molded composite plates as thin as stamped metal plates. More recently, however, these issues have been overcome, providing a clear advantage for composites over metals in high-temperature and low-temperature PEMFCs where power density is a secondary requirement. Chopped carbon fiber and graphite-filled/vinyl ester bulk molding compounds (BMCs) are finding wide use in bipolar plates for low-temperature PEMFCs. BMC cost has declined significantly as volumes have increased. Similarly, molding cycles once measured in minutes are now routinely completed in seconds, due to formulation improvements and the ability to make thinner plate cross sections.
- Chopped carbon fiber is also finding use as a porous paper backing material for gas diffusion layers in PEMFCs. Prepared by wet laying chopped PAN-based fibers, these can be manufactured in high volumes and low thickness. SGL’s (Wiesbaden, Germany) SIGRACET gas diffusion layers are being used by Hyundai Motor Group’s (Seoul, South Korea) new NEXO fuel-cell vehicle. Accordingly, SGL has increased SIGRACET production at its Meitingen facility.
- Toyota Motor Corp. (Tokyo, Japan) began selling its Sora fuel cell bus in March 2018, and it was the first such vehicle to receive type certification in Japan. The company plans to introduce more than 100 Sora fuel cell buses in Tokyo, ahead of the Olympic and Paralympic Games in 2020, and launched an updated version of the bus in August 2019. Teijin Carbon (Tokyo, Japan) announced it has developed a multi-material roof cover for the Sora comprising carbon fiber composites, aluminum and engineered plastics. The part is manufactured in one piece with complex shapes and is suitable for mass production.
- Hydrogen-powered fuel cells are also being developed for aircraft, with prototypes launched in 2019 by Alaka’i Technologies (Hopkinton, Mass., U.S.) and ZeroAvia (Hollister, Calif., U.S.). The Skai, developed by Alaka’i, features a carbon fiber composite airframe and landing skids, and is said to be the first eVTOL powered entirely by hydrogen fuel cells. ZeroAvia is flying a Piper Malibu refit with carbon fiber composite hydrogen tanks.
- Even though hydrogen fuel cells appear to be gaining momentum, the automotive industry, for now, continues to put more of its eggs in the battery power basket. Though some market analysts claim composites are not needed for battery electric vehicles, others disagree. “There are a lot of electric motor applications for CFRP with tremendous opportunities for us,” said James Austin in an interview during his tenure as president of North Thin Ply Technology(NTPT, Penthalaz-Cossonay, Switzerland), a developer of lightweight, spread tow and thin ply composite materials and manufacturing systems. “I think there is a lot more going on here than people appreciate. We think electric vehicles (EVs) will have a significant impact on the future of our company.”
- Another company supplying into battery boxes is SHD Composites (Sleaford, Lincolnshire, U.K.) with its prepregs using biobased polyfurfuryl alcohol (PFA) thermoset resin that meets phenolic performance. Its PS200 prepreg meets fire protection requirements for aircraft batteries mandated by the European Aviation Safety Agency (EASA), and is already in use at manufacturers of general aviation aircraft, where simulated battery fire testing showed an inside temperature of 1,100°C, while the outside never exceeded 250°C and the battery box never burned or decomposed. Composites Evolution (Chesterfield, U.K.) also supplies PFA prepregs reinforced with flax, glass, aramid, basalt or carbon fiber, and has passed flame, smoke and toxicity (FST) testing for aircraft and rail.
- Williams Advanced Engineering (Grove, Oxfordshire, U.K.), showcased structural CFRP battery box enclosures for its lightweight and scalable FW-EVX vehicle platform. Located within the car’s aluminum and CFRP monocoque are 38 battery modules, providing the EV’s power. Each 136-millimeter-wide battery module contains 10 pouch-type lithium ion batteries (think thin, as for a laptop) supplied by LG Chem (Seoul, South Korea). Pouches are stacked and protected within a CFRP box. Each of the 38 battery module boxes are made using flat CFRP sheet and the highly automated 223 process that Williams is patenting. Portions of the sheet for the box faces are cured, leaving flexible uncured hinges in between. These allow for folding of the partially cured sheet into a box, followed by final cure and bonding to produce a rigid enclosure. Each box is an impact-resistant, load-bearing exoskeleton, aiding in crash safety. The boxes are positioned and secured together to provide significant torsional and bending stiffness through the monocoque, which allows designers to reduce weight in other structures, increasing the vehicle’s fuel economy and performance.
Oil and gas
- Oil and gas: Flexible and light, thermoplastic composite pipe (TCP) is much more easily transported and installed in deep-sea applications than conventional metal pipe. Spooled here is 1.2 kilometers of a 6.7 ksi m-pipe, made by Magma Global.
- Not surprisingly, inherently corrosion-resistant composite materials are increasingly used to mold previously metal parts deployed in a host of offshore oil and gas drilling applications. Oceans are Earth’s largest naturally occurring corrosive environment, thanks to salt in seawater. Combined with man-made multipliers such as high temperatures and pressures and the host of aggressive chemicals, solvents and other fluids required to operate an offshore oil rig, and that’s a recipe for conditions that, over time, can be corrosive to almost any material — especially metals.
- Composite oil and gas parts include non-load-bearing topside platform components, such as fire-water mains, high- and low-pressure tubing, processing vessels and tanks, fire-blast panels, gratings and handrails, as well as newer subsea structures, such as carbon fiber rod umbilicals and components for protecting wellheads, manifolds and other equipment related to subsea processing. Composites also are making inroads into higher volume, more demanding offshore oil and gas applications, such as the systems of pipes with which producers explore for oil, find it and eventually bring it up from the wellhead to the surface. Although many are still in development — a process that includes a lengthy and rigorous qualification phase — the impetus behind this R&D is significant. The question is not if but when offshore oil operators will be compelled to make greater use of lightweight composites in structural undersea pipelines. This question is all the more critical as exploration companies develop subsea oil fields at greater distances from shore, and do so at unprecedented depths. In 2003 in the Gulf of Mexico, for example, only 35% of production was from wells at depths of more than 300 meters. By 2015, that figure was 95%. More to the point, more than 20% of Gulf wells are now at depths greater than 2,000 meters. At these depths, traditional steel pipe systems pose serious logistical problems and tally huge costs.
- Magma Global Ltd. (Portsmouth, U.K.) and Airborne Oil & Gas (AOG, Ijmuiden, Netherlands) are leading the way for development and qualification of thermoplastic composite pipe (TCP) for deep-sea applications, including a number of successful qualifications and pilot programs in 2018.
- In June 2019, Airborne Oil & Gas announced the successful completion of its first thermoplastic composite pipe (TCP) based on carbon fiber-reinforced polyvinylidene difluoride (PVDF) polymer. The company says this pipe provides a solution that doesn’t corrode, is resistant to CO2 and hydrogen sulfide (H2S), and is lightweight and spoolable, with a small bend radius. In 2019, several projects to qualify and build TCP deepwater risers, downlines or flowlines were announced, in Brazil, West Africa, Norway and more.
- Onshore, a composites-aided technology called hydraulic fracturing, often termed “fracking” or “frac’ing,” has been enabling the U.S. to increase its onshore oil and natural gas extraction over the past decade. The process artificially fractures low-permeability rock strata with explosives and then injects pressurized, sand-laced solutions into those fractures to facilitate oil and natural gas extraction. Each wellbore requires 10–40 multi-component tools called “frac plugs” (and accompanying “frac balls”) to stimulate multiple oil- or gas-producing layers, or “stages.” These critical parts are typically made with composites.
- In 2014, it was estimated that demand for these downhole parts exceeded more than 20,000 parts per week. Reportedly, in 2016, hydraulically fractured horizontal wells accounted for 69% of all oil and natural gas wells drilled in the US — about 670,000 of the 977,000 producing wells were hydraulically fractured and horizontally drilled. According to the U.S. Energy Information Administration (EIA, Washington, D.C.), in 2018 the total number of active oil and gas rigs working to drill new wells in the U.S. averaged 1,013, keeping the total count for 2018 on track to be the highest since 2014. As of July 2019, the number of active crude oil and gas rigs in the U.S. had reached 1,297. Alongside wind energy, the EIA predicts that natural gas will be the fastest-growing source of U.S. electricity generation in 2020.
- In 2018, Exel Composites’ (Vantaa, Finland) company Diversified Structural Composites (DSC) developed a fiber-optic-embedded carbon fiber composite rod for Ziebel’s (Tananger, Norway) well intervention system. The DSC-manufactured 6.2-kilimeter-long, 15-millimeter-diameter carbon fiber rod (the Z-Rod) is designed to deliver multiple fiber optic cables securely into a hostile downhole environment. Typically, the rod is deployed into a producing or injecting well for 48 hours, where the fiber optic sensors measure temperature and acoustic vibrations along its length. This enables a variety of applications — including flow allocation, fluid movement visualization, leak detection and stimulation fluid monitoring — which are valuable for optimal well and reservoir management.
Pressure vessels
- Display of a the carbon fiber pressure vessel for the hydrogen-powered Toyota Marai at the 2019 North American International Auto Show (NAIAS) in Detroit, Mich., U.S.
- High-pressure gas storage vessels represent one of the biggest and fastest-growing markets for advanced composites, particularly for filament wound carbon fiber composites. Although they are used in self-contained breathing apparatuses and provide oxygen and gas storage on aerospace vehicles, the primary end-markets for composite-reinforced pressure vessels are bulk transportation of compressed natural gas (CNG) products, and fuel storage in passenger cars, buses and trucks with powertrains dependent on CNG and hydrogen alternatives to gasoline and diesel.
Pressure vessels are organized into one of five types:
- Type I: All-metal construction, generally steel.
- Type II: Mostly metal with some fiber overwrap in the hoop direction, mostly steel or aluminum with a glass fiber composite; the metal vessel and composite materials share about equal structural loading.
- Type III: Metal liner with full composite overwrap, generally aluminum, with a carbon fiber composite; the composite materials carry the structural loads.
- Type IV: An all-composite construction, polymer (typically high-density polyethylene or HDPE) liner with carbon fiber or hybrid carbon/glass fiber composite; the composite materials carry all the structural loads.
- Type V: Linerless, all-composite construction.
Of these four vessel types, Type 1 has, by far, the largest market share at >90%. Type II vessels have about 4% market share, followed by Type III and Type IV, with Type V — a new designation — a distant fifth. However, in terms of material use, composites are the fastest growing material type, with 5.9% CAGR.
- Demand for alternative fuels is growing, in large part, because the extraction of natural gas from shale reserves has contributed to lower prices in North America and parts of Europe. In the North American market, for example, the cost of natural gas fuels currently runs about 36% less than diesel, per diesel gallon equivalent. In addition, increasingly stringent emissions regulations, including the EU Euro 6 Standard, which became effective earlier in 2016, are making diesel-powered buses and commercial vehicles more expensive for operators. Impending regulations are improving the marketability not only of CNG but also of hydrogen — after a period of relative dormancy — for fuel-cell powered vehicles.
- By 2023, the NGV population could be more than 65 million trucks, buses, and fork-lift vehicles. Based on strong demand in Argentina, Brazil, China, India, Iran, Italy and Pakistan, NGV deliveries could reach nearly 11 million per year by 2023. The vast majority (94%) of these NGVs are expected to be equipped with high-pressure (200+ bar) fuel storage systems.
- At CW’s Carbon Fiber 2017 conference, Chris Red of Composites Forecasts and Consulting LLC (Mesa, Ariz., U.S.) predicted that the demand for carbon fiber in composite pressure vessels will grow from 5.4 metric tonnes (MT) per year in 2016 to 26 MT/yr in 2021 and 45 MT/yr by 2025. At this 2025 volume, composite CNG and hydrogen cylinders for fuel cell vehicles (FCVs) will consume almost as much carbon fiber as projected for wind turbine blades, 50% more than forecast for automotive, rail and other ground transportation chassis and body components, and twice what is estimated for aerospace. Red cited forecasts for 2.1 million hydrogen FCVs to be produced from 2016 to 2025, corresponding to 3 million pressure vessels.
- Type IV composite pressure vessels used to store hydrogen are made by filament winding carbon fiber and epoxy over a plastic liner. Highly automated turnkey tank production lines are designed and produced by composites equipment suppliers including MIKROSAM (Prilep, Macedonia) and Roth Composite Machinery (Steffenberg, Germany), with the latter claiming it has accelerated hydrogen tank production 5–10 times with its new Rothawin technology. Cevotec (Munich, Germany) claims it can save 20% material and cycle time by using its fiber patch placement (FPP) system in dome areas. Cevotec’s CEO explains that working pressure of up to 700 bar in the tanks translates into ≈10 kilograms of carbon fiber for 1 kilogram of hydrogen storage — a very high ratio. FPP, however, applies carbon fiber in precise patches, designed to exactly cover the areas causing problems in filament winding. One FPP system is said to reinforce vessels for several winding machines.
- Hexagon Composites is a leading manufacturer pressure vessels, producing composite hydrogen storage tanks for cars and light vehicles in Raufoss, Norway, and Kassel, Germany, and tanks for its mobile pipeline system as well as for medium- and heavy-duty trucks and buses in Lincoln, Neb., U.S. It has vertically integrated through a merger with Agility Fuel Solutions (Costa Mesa, Calif., U.S.), sending tanks from Lincoln to Salisbury, N.C., U.S., where they are integrated into complete alternative fuel systems and installed on trucks and buses. Hexagon composite hydrogen storage tanks are also used on boats, ships and rail vehicles, as well as in stationary power systems, and are now being investigated for aircraft.
- In 2019, Agility Fuel Solutions announced it will supply 12 Type IV hydrogen fuel systems for Solaris Urbino 12 buses to be used in Bolzano, Italy. The developer of this new bus model, Solaris (Owińska, Poland), says it has reduced the mass of its bus fuel system by approximately 20% compared to the previous model.
- Hexagon claims to be the second largest user of carbon fiber in the world, but it will begin to face increased competition as Plastic Omnium (Paris, France), a world leader in plastic exteriors and front end modules for cars, has begun developing hydrogen storage tank and fuel cell capability. In 2017, it bought Optimum CPV, a Belgian company that makes composite hydrogen storage vessels, and Swiss Hydrogen, which works in fluid and thermal management. Further competition will come from Symbio, a 50/50 joint venture between French autocomposites manufacturer Faurecia (Nanterre) and tire producer Michelin (Clermont-Ferrand), announced in March 2019 with the aim to create a world leader in hydrogen fuel cell systems. Faurecia has invested $28 million in its global center of expertise for hydrogen storage systems at its R&D campus in Bavans, France. It also announced it would work with Airbus composite fuselage supplier Stelia Aerospace (Toulouse, France) to develop high-pressure carbon fiber composite hydrogen tanks for fuel cells. Announced in Sept. 2019, Voith Composites (Heidenheim, Germany) and composites solutions provider HRC (Shanghai, China) will also partner to develop next-generation high-pressure hydrogen storage vessels for fuel cell vehicles.
- Currently, 13 automotive OEMs have fielded FCV demonstrators and test fleets. Further, at the 2019 North American International Auto Show (Detroit, Mich., U.S.), Toyota exhibited its new Mirai fuel cell electric vehicle (FCEV), which is currently on the market and for sale. It offers 67 mpge fuel efficiency, a range of 312 miles and has a manufacturers suggested retail price (MSRP) of $58,500.
- Linerless, all-composite pressure vessels, which fit the more recent and radical Type V classification and are best able to reduce mass in weight-sensitive applications, are the goal for a number of pressure vessel manufacturers. Infinite Composites Technologies (ICT), Tulsa, OK, US) offers one of a growing number of Type V vessels coming to market. The company’s patented infinite composite pressure vessel or infiniteCPV (iCPV), an all-composite design, enables users to take advantage of the maximum fuel storage capacity by reducing vessel weight. The iCPV provides 10% more usable volume and reduces vessel weight by 90% compared to conventional vessels. While the company has a focus on developing next-generation fuel storage and delivery systems for natural gas vehicles and storage applications, it also hopes to introduce its Type V tank technologies to the commercial space industry.
- A growing and likely huge, sustainable market for pressure vessels is the construction of seawater reverse osmosis (SWRO) desalination plants. SWRO depends on membrane systems that serially cleanse water piped onshore from the ocean (See “Utility Infrastructure”). These membranes must be encased in membrane housings. Filament-wound fiberglass pressure vessels are used almost exclusively for this purpose today, in quantities of as many as 6,000 per desalination plant. The Freedonia Group (Cleveland, Ohio) predicts demand for SWRO housings and related equipment will increase 6.9% per year. In the US alone, the market was worth about US$495 million in 2017.
Renewable energy
- Growth in wind energy: During the second quarter of 2019, 736 megawatts of new wind power capacity were installed in the U.S. The industry commissioned 1,577 megawatts in the first half of the year, a 53% increase over the first half of 2018.
- Wind energy continues to dominate in this segment and remains, far and away, the world’s largest market for glass fiber-reinforced composites. It’s also competing with other heavy users — such as the aerospace industry — for carbon fiber use as blades get longer and blade builders look for ways to lightweight the massive structures without sacrificing performance. Wind turbine blades remain a key market segment for composites.
- According to a report titled “Wind Turbine Composite Materials Market (Type: Glass Fiber, Carbon Fiber, Others; Application: Wind Blade, Nacelle, Tower, Base, Others; Manufacturing Process: Resin Infusion Technology, Prepreg, Hand Lay-up, Others) — Global Industry Analysis, Market Size, Opportunities and Forecast, 2017–2023” by Acumen Research and Consulting, (Maharashtra, India), the global market for wind turbine composite materials could reach a value of more than $12 billion by 2023 and is expected to grow at a CAGR of 9.6% until 2023.
- According to a report by the American Wind Energy Assn. (AWEA, Washington, D.C., U.S.), U.S. wind capacity has increased nearly fourfold in the last 10 years, climbing to 96,433 megawatts. During the second quarter of 2019, 736 megawatts of new wind power capacity was installed in the U.S. The industry commissioned 1,577 megawatts in the first half of the year, a 53% increase over the first half of 2018.
- The roster of U.S. wind projects under construction and in advanced development, as of the end of the second quarter of 2019, had reached 41,801 megawatts, a 10% increase year-over-year, according to AWEA’s “US Wind Industry Second Quarter 2019 Market Report.” According to AWEA, project developers signed 1,962 megawatts of power purchase agreements (PPAs) during the second quarter of 2019, contributing to a total of 4,799 megawatts for the year.
- Some of this growth is likely driven by the U.S. production tax credit (PTC), a federal subsidy that provides a per-kilowatthour tax credit for the first 10 years of a wind farm’s operation. The current PTC was passed in 2016 and provided a 2.3 cents/kilowatthour credit. The PTC credit decreases incrementally each year until its expiration at the end of 2020. It is unlikely the PTC will be renewed as the wind energy industry is clearly capable of standing on its own without subsidy.
- As for offshore wind in the U.S., there was a total potential offshore wind pipeline of more than 25,000 megawatts spanning 10 states off the East and Great Lakes coasts at the end of 2018.
- The global wind market is growing quickly, expanding 9.5% in 2018. According to AWEA, there are now 591 gigawatts of wind farms generating electricity worldwide.According to the Global Wind Energy Council’s (GWEC) 2018 Global Wind Report, 51.3 gigawatts of new wind energy was installed in 2018–46.8 gigawatts onshore and 4.5 gigawatt offshore — , a slight decrease of 4.0% compared to 2017, but still a strong year. GWEC says annual installations have topped 50 gigawatts each year since 2014, despite ups and downs in some markets. China continues to lead the offshore wind market with 21.2 gigawatts of new wind installations in 2018. The country has led market since 2008 with a current total of 206 gigawatts of onshore wind. The second largest market for onshore wind in 2018 was the U.S. with 7.6 gigawatts of new installations and current total of 96 gigawatts onshore. As for offshore wind, China installed 1.8 gigawatts in 2018, taking the lead for the first time, followed by the United Kingdom, which installed 1.3 gigawatts in 2018. Globally, the share of offshore installations in the overall wind market continues to grow, reaching 8% for new installations and 4% of the total installations in 2018.
- The size of wind turbines continues to increase as well. Twenty or more years ago, when the first large-scale, commercial wind-generated power came on line, wind farms comprised turbines rated at 1 megawatt or less, with glass fiber-reinforced blades that typically ranged from 10–15 meters long. Today, offshore, 6–9-megawatt turbines with blades 65–80 meters long are the norm.
- In September 2018, MHI Vestas announced that its V164 turbine platform had achieved a power rating of 10 megawatts, making it the first commercially available double-digit wind turbine. While 10-megawatt turbines won’t be installed until 2021, an 8.8-megawatt version of the V164 was deployed in Vattenfall’s (London, U.K.) European Offshore Wind Deployment Centre (EOWDC) in Scotland’s Aberdeen Bay in April 2018. The turbine has a tip height of 191 meters and each blade is 80 meters long.
- In early 2019, Siemens Gamesa Renewable Energy (SGRE, Zamudio, Spain) launched the SG 10.0–193 DD, the company’s first 10+ megawatt offshore wind turbine. It features 94-meter-long blades — each the same length as one soccer field — providing a swept area of 29,300 square meters. The annual energy production of one SG 10.0–193 DD is said to be sufficient to supply about 10,000 European households with electricity. In addition, Siemens Gamesa is constructing the world’s largest wind turbine blade test stand in Aalborg, Denmark. The site will be capable of performing full-scale tests on the next generations of SGRE rotor blades and is expected to be fully operational before the end of 2019. The first tests will reportedly be on the 94-meter-long blades for the SG 10.0–193 DD offshore wind turbine.
- The largest and most powerful wind turbine in development is the Haliade-X, which is being developed by GE Renewable Energy (Paris, France). Towering 260 meters over the sea (more than five times the height of the iconic Arc de Triomphe in Paris, France) the Haliade-X 12 MW carries a 220-meter-diameter rotor. Designed and manufactured by LM Wind Power, the 107-meter-long blades will be the longest offshore blades to date and will be longer than the size of a soccer field. GE revealed the first nacelle for the Haliade-X 12-megawatt offshore wind turbine in July 2019, at its production site in Saint-Nazaire, France. GE says this is a step towards launching the Haliade-X to the market in 2021.
- As wind turbines get larger and blade lengths continue to increase, carbon fiber reinforcement in spar caps — incorporated as the reinforcing member of wind turbine rotor blades — has become an efficient way to reduce overall weight and increase blade stiffness to prevent tower strikes in the event of sudden wind gusts. According to Philip Schell, executive VP, carbon fiber, Zoltek Corp. (St. Louis, Mo., U.S.), roughly 25% of wind turbines are now manufactured with carbon fiber spar caps. Although that figure is trending upward, it also underscores that most turbines are still built entirely from glass fiber composites. He adds that when all cost/performance trade-offs are considered, a solid case can be made for substituting carbon fiber for glass fiber in the manufacture of spar caps for turbine blades 55 meters long and longer.
- In June 2019, SAERTEX (Saerbeck, Germany) announced its infusion-optimized unidirectional, 618-gsm, non-crimp carbon fiber fabric was used to produce a prototype 87.5-meter, 800-millimeter carbon fiber spar cap made using vacuum infusion technology. According to SAERTEX, the spar cap, completed in April by a wind turbine blade manufacturer in China and was designed by WINDnovation Engineering Solutions (Berlin, Germany), is the longest ever produced.
Sports and recreation
- Sports and recreation: In 2019, Arevo unveiled the world’s first 3D-printed carbon fiber unibody production bike frame.
- The sporting goods market was a boon to the advanced composites market in the final decade of the 20th century. Carbon fiber fishing rods were introduced to great fanfare — and sales. Golf shafts and tennis rackets weren’t to be left out, and driven by the growing popularity of cycling races like the Tour de France, carbon fiber bicycles went from pro racing to bike trail and street, and saw numerous innovations in the 1990s and 2000s, in materials and fabrication methods.
- The use of lightweight and high-performance materials in sports equipment continues to increase. According to a market report published by market research firm Lucintel (Irving, Texas, U.S.) in early 2019, the use of composite materials in the global sporting goods industry continues to grow, is expected to reach an estimated $579 million by 2023 and is forecast to grow at a CAGR of 3.2% from 2018 to 2023. Opportunities exist in a range of products including surfboards, skis and snowboards, bicycles, rackets, golf clubs, hockey sticks and fishing rods. Carbon fiber-reinforced polymer (CFRP) composites are expected to remain the largest segment over the forecast period, with glass fiber composites experiencing moderate growth as well.
- Bicycles continue to be the highest-profile market for composites use. In 2019, Arevo (Milpitas, Calif., U.S.) unveiled the world’s first 3D-printed carbon fiber unibody production bike frame at Eurobike 2019 in Friedrichshafen, Germany. The company also produces a 3D-printed thermoplastic rim. The bicycle components were produced via the company’s “Arevo DNA” technology, which is an additive manufacturing (AM) process featuring patented software algorithms that are said to enable generative design techniques, free-motion robotics for “true 3D” construction, and direct energy deposition for virtually void-free construction optimized for anisotropic composite materials. Arevo says its process takes the design and final manufacture of a bike frame from 18 months to a few days, and results in significantly reduced production costs. Additional benefits are said to include the capability for serial, volume production of AM-made composite parts, automation and the ability for localized “on-demand” manufacturing and customization.
- The challenge the bicycle manufacturing industry faces, as reported in CW, is the lack of strictly enforced standards for the design and fabrication of carbon fiber composite bike frames. The lack of standards and oversight can and has led to substandard product quality, resulting in injury or death due to failure of composite structures. No legally binding structural safety standards yet exist that address common rider load and environmental conditions (braking, impact loads, fatigue, vibration, material aging or degradation, material abrasion and wear) for high-performance composite bikes. Further, the existing ASTM D-30 test methods are not yet recognized by ASTM’s F-08 Bicycle Committee.
- The International Organization for Standardization (ISO, Zurich, Switzerland) published its ISO 4210 standard for bicycles — the most current standards for bicycle manufacture — in 2014 and 2015 in nine sections. ISO 4210 was “developed in response to demand throughout the world, and the aim has been to ensure that bicycles manufactured in compliance with this International Standard will be as safe as is practically possible. The scope has been limited to safety considerations and has specifically avoided standardization of components,” according to ISO.
- With that said, there are plenty of bicycle manufacturers that take safety seriously. A good example is HIA Velo (Little Rock, Ark., U.S.), which combines composite materials to make its products more durable. HIA Velo worked with Innegra Technologies (Greenville, S.C., U.S.) to incorporate Innegra S high-modulus polypropylene fabrics, sized for compatibility with epoxy resin, to discrete areas of the Alfa bike frames to improve frame durability. Similarly, Derby Rims LLC (San Anselmo, Calif., U.S.) makes bicycle rims (wheels) that combine carbon fiber and high molecular weight polypropylene (HMWPP) for greater toughness.
- In watersports, ecological responsibility and sustainability continue to be a focus, and many fabricators are employing natural or reclaimed fibers and bio-composites. A good example is Cobra International (Chonburi, Thailand)., which is known for its sustainable technologies and products. Its CocoMat coconut fiber technology and bio-based surfboards meet the highest ECOBOARD requirements set by Sustainable Surf and carry the ECOBOARD GOLD logo.
- A growing trend toward customization, and high-end manufacturers’ desires to cater to the unique needs and desires of individual athletes, has opened the door to 3D printing. Krone Ltd. (Dallas, Texas, U.S.), for example, is employing the process in the manufacture of its top-end golf clubs. Faced with exacting limits of club size and weight, and increasing demand from golfers for improved driver performance (ball distance, loft, speed and spin), “feel” and balance, company founder Mark Kronenberg approached the CRP Group (Modena, Italy), which had years of experience with 3D printing in Formula 1 racing. CRP Group companies include CRP Technology, which produces additive manufacturing materials and technology, and CRP Meccanica, with high-precision CNC machining experience.
- The three companies worked together to develop the KD-1, a composite driver club head that consists of an additively manufactured body, using selective laser sintering (SLS) and employing Windform SP, a sinterable carbon fiber/polyamide powder; a Ti6A14V titanium strike face, CNC-machined from billet material, followed by sandblasting and cleaning; and a brass weight, also CNC-machined and sandblasted. Printable in hours, the hollow body’s lattice geometry optimizes its stiffness, while the carbon fiber/polyamide exhibits high ductility and impact absorption. The machined titanium face fits over and is adhesively bonded to the body. Four Helicoil inserts in the body, opposite the face, accept fasteners that attach a brass weight. According to Krone, the AM process coupled with CNC reduces the touch labor otherwise required for conventional composite driver heads made with prepreg, and produces parts with tighter tolerances than those made from cast and forged metals, without time- and labor-intensive secondary operations.
Utility infrastructure
- Utility infrastructure: Mitaş Composites can filament wind composite lighting poles up to 12 meters long and 800 millimeters in diameter.
- According to the American Iron and Steel Institute, there are about 185 million utility distribution poles in North America, and an estimated 2.5 million wood poles are replaced annually. These poles support power and telecommunications lines. Wood poles are commonly replaced due to age, damage and decay. Fiber-reinforced polymer (FRP) composite poles were developed in the 1960s to address these shortcomings, first installed in Hawaii as a solution to wood pole degradation and steel pole corrosion. Composite poles are more environmentally friendly because they don’t require the use of toxic chemical preservatives like creosote, pentachlorophenol or copper compounds. This chemical treatment also makes disposal of used wood poles very expensive. Although steel poles offer 60–80 years of service compared to 40–50 years for wood, as well as lighter weight, higher stiffness and lower maintenance, they also must be galvanized or coated to prevent corrosion and are also conductive, difficult to repair and harder to drill in the field for climbing access and installation. Composite utility poles offer the longest life, lowest maintenance, lightest weight and ability to drill for ease of installation.
- Composite poles currently account for less than 1% of the overall utility pole market according to Lucintel (Dallas, Texas, U.S.), but their share is expected to grow from $228 million in 2018 at an annual rate of 5.7% to reach $318 million in 2024. Power transmission and distribution currently accounts for approximately 71% of the global composite pole market, but lighting, which comprises 23%, is likely to experience a relatively higher growth rate, fueled by the replacement of traditional materials.
- In 2019, BASF Co. Ltd. (Shanghai, China) announced that its Boldur utility poles, produced via filament winding with the company’s Elastolit polyurethane (PU) and continuous glass fiber, are now available and are being used by a utility pole distributor in Japan. The ultra-light poles are said to withstand severe weather conditions and maintain reliable electricity supply in areas affected by natural disasters.
- Mitaş Group (Ankara, Turkey), a manufacturer of steel towers, distribution and transmission poles, and substation structures for the energy market, has invested in a filament winding production line for manufacture of composite utility poles. The automation-ready equipment, with a manufacturing capability of 1,000 poles per month, makes Mitaş one of Turkey’s first manufacturers of composite utility poles and is enabling the group to grow and diversify its existing product range.
- Composites’ superior strength are also fueling their growth in transmission cables. Aluminum conductor composite core (ACCC) cable for power transmission lines is produced by CTC Global (Irvine, Calif., U.S.). Compared to traditional aluminum conductor steel-reinforced (ACSR) cables, ACCC cables feature a carbon fiber composite rod pultruded with a thin sheath of insulating glass fiber composite to prevent galvanic corrosion with the aluminum overwrap. ACCC cable’s strength to weight ratio is roughly six times better than steel, with a coefficient of thermal expansion about ten times lower. ACCC cable also reduces power losses by 25–40%. With traditional cables, up to 25% of power is lost simply from transmitting electricity over long distances.
- Similarly, Celanese Corp. (Dallas, Texas, U.S.) and Southwire Co. LLC (Carrollton, Ga., U.S.), North America’s largest wire and cable producer, co-developed the C7 Overhead Conductor, featuring a lightweight and high strength-to-weight, multi-element composite core of Celstran continuous fiber-reinforced thermoplastic rods (CFR-TPR), made by Celanese. The C7 Overhead Conductor reportedly not only increases capacity, but provides cost-avoidance benefits by obviating the need for new towers and poles, a need that would have to be met if increases were attempted with traditional steel-cored conductor cables. It also nearly doubles the transmission capacity, yet exhibits less sag than an aluminum conductor steel-reinforced (ACSR) cable of the same diameter.
- In addition, composites can play an important role in refurbishing America’s aging underground potable water infrastructure by providing corrosion-resistant, durable and long-lasting underground pipe solutions. One example of composites put to use for piping was a water project in the Middle East. The selected pipe for the project was Amiantit Europe’s (Mochau, Germany) pipe product, Flowtite Grey, which was intended for water, sewage, waste and raw material management.
- The 22nd Annual Underground Construction Municipal Sewer and Water Survey, conducted by Underground Construction magazine (Oildom Publishing Co., Houston, Texas, U.S.) and published in February 2019, indicates the strongest industry projections in many years, with every category showing growth. New installation of sewer infrastructure is projected to increase by 3.7% in 2019 to $5.4 billion, with a 3.9% increase ($3.85 billion) for water construction. Rehabilitation continues to outpace new construction with sewer rehab projected at 4.1% growth or $4.9 billion in 2019, and water growing 4.5% to $2.2 billion. Projected spending plans for U.S. sewer, water and stormwater piping infrastructure total $19.75 billion for 2019, representing an overall increase of 3.7%.
- This survey also measured impacts from trenchless construction and rehabilitation methods, in which composite materials are used to reline existing pipes (cured in-place pipe, or CIPP). During budget-crunching times, trenchless rehabilitation gained ground as a cost-effective and successful stop-gap measure to stretch dollars. As a result, trenchless work has gained a foothold in all aspects of construction and rehabilitation in the US and abroad. The survey revealed that 52% of cities prefer to use trenchless CIPP for rehab, and for new construction, trenchless is used in about 25% of projects.
- In 2018, the Innovative Materials for America’s Growth and Infrastructure Newly Expanded (IMAGINE) Act was introduced as a bill to the U.S. Congress, designed to promote the increased use of innovative materials, such as composites, in infrastructure projects.
- In the meantime, filament wound fiberglass/polyester composites have found broad application in several stages of seawater reverse osmosis (SWRO) desalination. SWRO plants around the world use many miles of corrosion-resistant fiberglass-reinforced polymer (FRP) low-pressure piping as a distribution network, primarily over land, to carry seawater to the plant, to distribute the potable water that is produced, to carry the brine (salt and impurities) back to the ocean, and for internal plant treatment piping and energy-recovery devices. Fiber-reinforced plastic also forms storage tanks and piping used in desalination plants to contain sodium hypochlorite (NaOCl) used in chlorination of desalination process water, and for sulfuric acid — very difficult to store in metal but readily handled in fiberglass/epoxy vinyl ester tanks and piping at ambient temperatures and concentrations below 50%, according to corrosion industry resin producer Ashland.
- Using fiberglass tanks to fight corrosion, however, introduces the possibility of an electrostatic charge being generated when filling or emptying tanks, particularly those containing petroleum-based liquids, because the product movement can create a static charge between the liquid and the tank wall. To address this risk, fiberglass tank manufacturers have historically used anti-static fillers in the resin, typically carbon black or conductive mica, to dissipate any static charge. But, filler ratios up to 30% are often necessary, which makes wetout of the fiberglass more difficult and slows the resin cure rate. Use of TUBALL graphene single-wall carbon nanotubes supplied by OCSiAl (Leudelange, Luxembourg and Columbus, Ohio, U.S.) can provide electrostatic discharge (ESD) protection by dissipating electrostatic charge inside and outside a storage tanks.
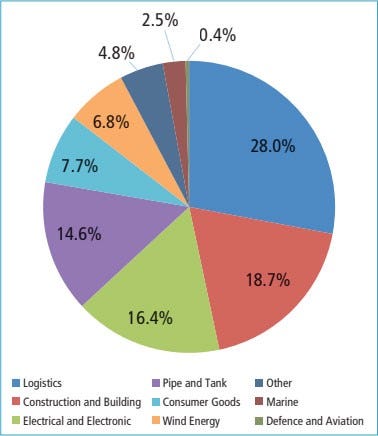
- A review of the applications of the composites industry within the global composites market reveals that the top four industries in terms of volume are transportation, construction and building, electrical and electronic goods and the pipe and tank manufacturing industries. In terms of value, the top four industries which employ composite products are transportation, construction and building, electrical and electronic goods and the defense and aviation industries. The most remarkable industry among these is the defense and aviation industry. The defense and aviation industry, which ranks in final position in terms of volume, with only 0.4 percent by mass, is among the top three industries in terms of value, representing 13 percent of the market, indicating the high value-added nature of the composite products employed within the industry.
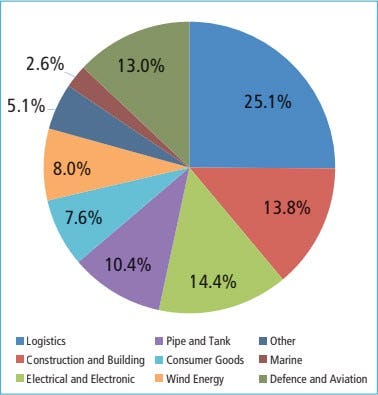
- The development of the composites industry will vary depending on the relevant fields of application. While the growth rate in the maritime, construction and building and consumer goods industries is expected to see a growth rate of 0 to 2 percent; the growth rate in electrical and electronic goods, pipe and tank manufacturing, transportation and aerospace and aviation industries is estimated to be from 3 to 7 percent. The sale of composites to the wind power industry is expected to grow by 15 to 20 percent on a year-on-year basis with an optimistic perspective.
- It is noted from a review of unit prices in 2019 that the composite materials used in the defense and aviation industries have a high added value

In 2019, the Asian market, with 5.2 million tons, held the largest market share, accounting for 47 percent of the global market in terms of volume and 43 percent in terms of value. The Chinese market alone accounts for 28 percent of the global market, or 3.1 million tons. The North American market, with 2.8 million tons, accounted for 26 percent of the global market in terms of volume and 30 percent in terms of value. The European market accounts for 21 percent of the global market in terms of both volume and value. The African and Middle Eastern market, with 0.4 million tons, accounted for 4 percent of the global market in terms of both volume and value. Finally; the South American market accounted for 2 percent of the global market, at 0.2 million tons.
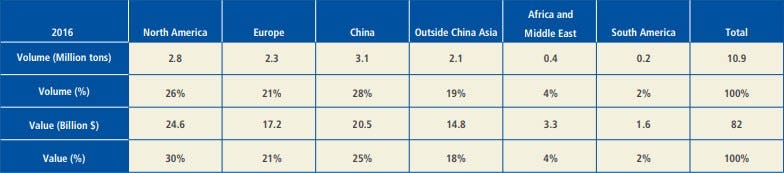
- The global composites industry is predicted to grow by 4 percent on average on a year-on-year basis between 2019 and 2025. It is predicted that growth in China, which is expected to grow by 7 percent, will account for 60 percent of the said overall growth rate. Such a growth rate is larger than China’s overall growth rate between 2010 and 2019, which was a combined total of 57 percent. The rest of the Asian market will grow by 3 percent on a year-over-year basis in the forthcoming period, contributing to the overall growth by 17 percent. It is predicted that the North American market will grow by 2 percent on a year-on-year basis, accounting for 11 percent of overall growth in the forthcoming period. The forecast for the growth rate on a year-on-year basis of the European market is 1 percent for the period between 2019 and 2025. Thus, the European market will maintain its share of 6 percent within overall growth. The share of the Asian market constantly grew between 2010 and 2019, as its market share, which was 45 percent in 2019, grew to 47 percent in 2018 and 2019. It is expected to attain 52 percent by 2025.
- In next Table, the distribution by industry of the composites market in terms of volume is examined. It is indicated that, in terms of volume, some 67 percent of the composite materials used in the transportation industry are used in North America and Europe, while 60 percent of the composite materials used in the construction and building industry were used in North America and China, and that North America holds a dominant share in terms of the use of composite materials in the maritime industry as well as the defense/aviation industry.
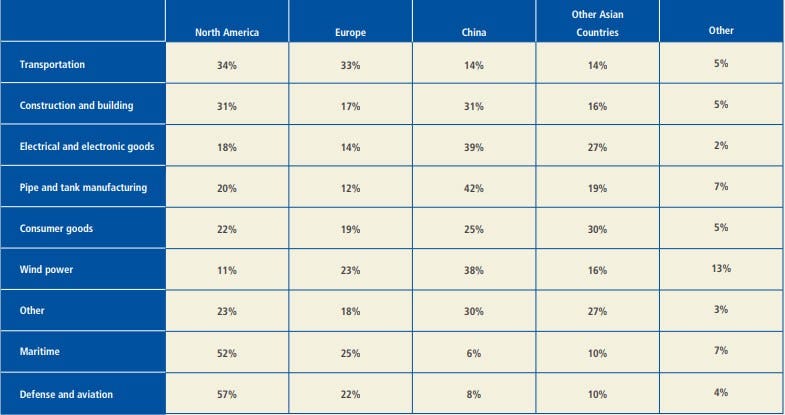
- In 2019, the most commonly used composite materials in terms of volume worldwide were thermoset resins as matrix and glass-fiber, a low added value product, as a reinforcing agent ( next Table ). Furthermore, the distribution of the processes employed to derive composite materials is provided within next table.
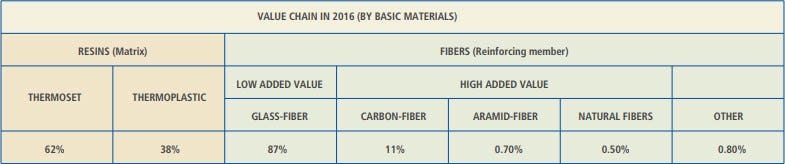

Competitive Landscape and Composites Market Share Analysis
- Composites competitive landscape provides details by vendors, including company overview, company total revenue, market potential, global presence, Composites sales and revenue generated, market share, price, production sites and facilities, SWOT analysis, product launch.
The key market players for global Composites market are listed below:
- 3M
- Asahi Fibreglass
- Aertex Group
- Acordis BV
- AKSA
- Advanced Glass Fibre Yarns
- Braj Binani Group
- Airbus
- Axalta Coating Systems
- BOC
- Formosa Plastics Corporation
Composites Market segment by regions
- North America (United States, Canada and Mexico)
- Europe (Germany, France, United Kingdom, Russia and Italy)
- Asia-Pacific (China, Japan, Korea, India, Southeast Asia and Australia)
- South America (Brazil, Argentina)
- Middle East & Africa (Saudi Arabia, UAE, Egypt and South Africa)
Indian Composites Market
- The Inidian composites industry, which is comprised of some 700–800 companies at least partially engaged in the composites business, 180 of which are medium- and large-sized companies, employing roughly 8,200 people, produces products with a high added value.
- Currently; the value of the Indian composites market has reached €1.4 billion ($1.65 billion) and the volume of the same has reached 265,000 tons. The composites industry in India is growing by way of gaining market share from replacement materials as it does in the rest of the world.
- The composites industry is growing in India at a higher rate than it is in Europe and elsewhere in the world. The India composites industry has developed rapidly, and in the long term, as the case is with the other industries, it has developed in line with global economic developments, leveraging the effects of the dynamics within the country. The industry grew by 8 to 12 percent on a year-on-year basis in India over recent years in line with then-prevailing economic conditions. The growth rate in 2019 has been 6 percent.
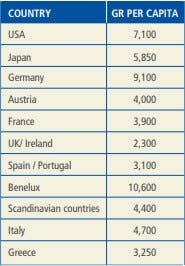
- A review of composites consumption per capita, which is globally recognized as a “Development Criterion”, reveals that India is looking at considerable opportunities in respect of the composites industry. The said amount, which ranges between 4kg and 10kg across the world, is 3.4kg for India. The average unit price, which is around €6.9/kg ($8.1/kg) globally, is roughly €5.3/kg ($6.2/kg) in India. Both the consumption amount per capita and the average price in India are considered advantages for the country in the forthcoming period. In terms of volume; composite products are most commonly used in pipe and tank infrastructure (36%), the transportation and automotive (24%) and construction and building (21%) industries in India . The acceleration of the production in India of high-tech products is expected to increase the amount and the percentage of composite materials used, particularly wind power, aerospace and aviation as well as the electrical and electronic goods industries.

- Also, the other composite applications with high growth potential include carbon fiber applications, pipe applications, automotive and transportation, greenhouse applications, solar panels, construction reinforcements, window and door applications, Polypropylene Random Co-polymer (PPRC) heating pipes (for boilers), engineering plastics and maritime applications.
- There is a considerable distance India must cover with respect to the production of machine-driven and high-tech products. Glass-reinforced plastic (GRP) pipe production, the growth rate of which has reached 36 percent, leveraging demand in India and in surrounding countries, will continue being the driving force of the Turkish composites industry. Pultrusion, hot press molding (HPM) roll-up — hot press molding compound (BMC) and thermoplastic injection processes are expected to increase their market shares in the forthcoming period. Resin transfer molding (RTM) will continue its growth especially in wind power, maritime, automotive and transportation as well as the water slide industry.
- Composite materials enjoy an advantageous position relative to the conventional materials of steel, aluminum and metal alloys for their high level of strength, light weight, design flexibility, capability of maintaining their form and functionality, electrical insulation, long service lives due to their being stainless and corrosion-resistant, the ability they offer to mold numerous parts which are monitored in conventional materials into a single piece instead of being designed in multiple pieces and subsequently assembled, as well as the ability to apply the desired color to the product during molding and to use the same for a long period of time without the need for maintenance, and the fact that the equipment chosen for production is cheaper irrespective of the selected molding method. Hence, over 50,000 successful applications that have so far emerged. The growth of the composites industry and the increase in the export levels of the same will enable India, which produces a considerable portion of the relevant raw materials, to gain an advantage in global competition.
- State-sanctioned market creation efforts such as the most recent wind power plant tender will accelerate the growth path of the industry, and will offer significant advantages to the companies that operate in the industry.
- The composites industry falls into the scope of the chemistry industry on account of polyester, vinyl esters, epoxy and similar other resins being the main raw materials of thermoset products; into the scope of the plastics industry on account of polyamide (PA), polypropylene (PP), polycarbonate (PC) and other similar thermoplastics being the main raw materials of thermoplastic products; into the scope of the textiles industry on account of the technical textiles that are manufactured by way of the weaving and knitting of glass fibers, carbon fibers and aramid fibers; into the scope of the glass industry due to glass fiber production and certain other industries on account of the finished composite products that are employed in automotive, defense, aviation, construction, sports, entertainment, consumer goods and other similar industries.
- The growth course of the composites industry is generally above that of global economic growth. This course will also remain unchanged in the forthcoming period.
- The composites industry is a crucial industry for India, since it produces high added-value products and composites are the materials of the future. It would be useful for governments, local governments, investors and industrialists to demand and prefer lighter composite material alternatives with longer service lives and higher strength, which offer more contemporary solutions, both for the benefit of such governments, local governments, investors and industrialists and for the benefit of the national economy. Currently, a decrease in the amount of energy and fossil fuel consumption in both the aviation and aerospace industries and the automotive industry is entirely and directly connected to the penetration into those industries of composite materials. It is estimated that this process will develop further, serving the interests of the composites industry, being an industry that offers inputs to and generates solutions for almost all other industries.
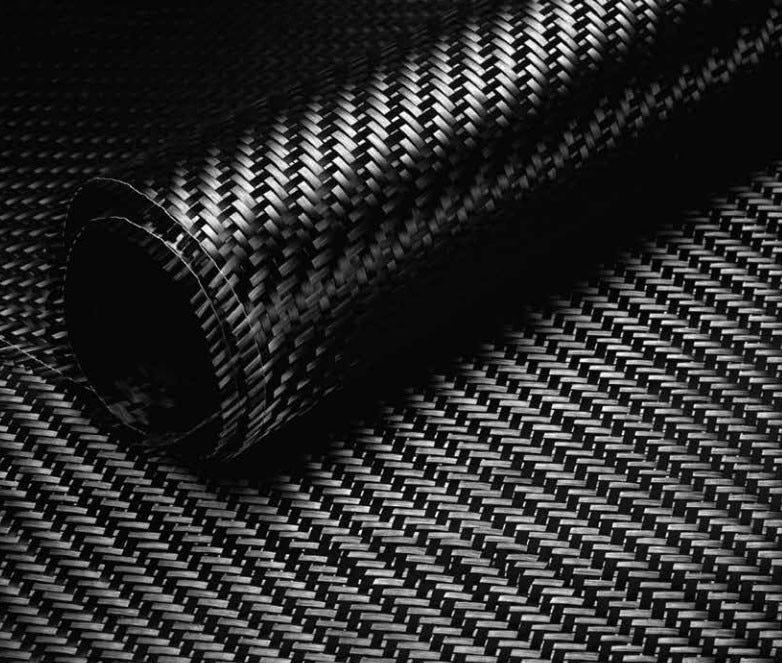
- In that regard; it is considered that, as composite materials are used more effectively and prevalently in India, composites production in India will also be able to grow in high added-value industries; that, as the production of advanced composites becomes prevalent in India, India’s export potential to not only Europe but also the entire world will increase, and the industry will contribute to covering India’s trade deficit.
- Glass fiber (87%) and carbon fiber (11%), currently the most commonly-used reinforcement materials in the world, are both produced in India. In respect of resins; while unsaturated polyester resin and vinyl ester resin are produced in India, epoxy resins and thermoplastic resins are imported. Styrenes, phtalics, maleics and glycols, which are used for unsaturated polyester production, are not produced in adequate volumes in India, so the need for the said items is covered entirely by way of imports. As the production of technical textiles, which are used for composite production, has grown in India, the industry is now able to cover all its needs from the domestic market. The figures indicate that the composites industry currently exports some €250 million ($294 million) worth while it imports some €250 million worth.
- The Indian composites industry, which imports the chemical raw materials needed and exports the reinforcing materials and resins as well as technical textiles and finished products produced in India, and which, therefore has helped balance foreign trade, and has gained a reputation in the international arena for the Turkish companies that undertake and carry out major contracts worldwide.
- The composites industry exports goods both directly and indirectly. While directly exporting the raw materials, industrial intermediate goods and finished products produced thereby through contracts awarded and projects undertaken, the industry also indirectly exports its production outputs as parts of each automobile, bus, boat, bathtub etc. exported. The industry exports its production outputs essentially to European countries, Russia, the Turkic Republics, the Middle East and North Africa. Endeavors to increase the number of export destination countries and to cover new markets are increasingly being carried out. Certain companies in the industry export their products all over the world, including the United States and even to Far Eastern countries.
Reliance Industries signs pact with German co to sell wood alternatives in India
- RIL has signed a license deal with Resysta International GmbH to exclusively make and sell the German firm’s natural fibre polymer composite in the country.
- The product, namely RelWood, is the raw material for the production of sheets and various products used in a wide range of wood and plywood replacement applications, according to a statement by RIL.
- Through this strategic partnership with Resysta, RIL looks forward to producing the RelWood compound exclusively to meet the fast-growing demand of a real alternative to tropical wood. Resysta is a leading German innovator, and together we will offer Indian consumers cutting edge technological product as an alternative to natural wood.
- RelWoodTM looks and feels like wood but is made of composite natural fibres, polymers and a specialized blend of additives. The company said that RelWoodTM is more durable than wood, and does not require any trees to be felled.
- We are currently licensing our technology across the world, and have found in RIL our perfect partner for India. By manufacturing the Resysta Compound locally, the products become even more environment-friendly and easily available.
- The market for wood materials in India is estimated at Rs 80,500 crore (or 30.8 million tonnes) with tropical wood having the largest share in volume and value terms, growing at 10% annually. International companies such as Armstrong and Pergo have entered the market for alternative wood by forming strategic alliances with local players to tap the potential.
- RIL will sell the product to the construction sector and the furniture industry and anticipates demand arising out of the government’s smart city project.
Reliance Ind acquires Kemrock in auction-sale by banks
- RIL has bought over distressed bank assets of Vadodara-based Kemrock Industries and Exports Ltd, a plastics and composites maker, through an e-auction.
- The company was put up for sale by Allahabad Bank, the leader of a consortium of 11 banks.
- While RIL did not disclose its winning bid’s size, the auction notice by the lenders put the reserve price for the asset at just over ₹673 crore.
- The sale, carried out under the SARFAESI Act, was by Allahabad Bank, JM Financial Asset Reconstruction Company and Edelweiss Asset Reconstruct Company (assigned from other lenders), Karur Vysya Bank, Union Bank of India, State Bank of India and ICICI Bank.
- The notice also gave the claim amount from the asset to be ₹1,652.18 crore. Other claims against the company included ₹1.41 crore by the EPFO, ₹205.77 crore by the Central Excise and Customs Department and a VAT liability of ₹82.16 crore.
- Kemrock manufactured fibre-reinforced composites that were used for the aerospace industry. A 2013 news report by Reuters quoted Kalpesh Patel, CMD, Kemrock, saying that the factory was running at just 15–20 per cent capacity as banks refused to lend further working capital to the business.
- He said that he was at the time looking for the US-based distressed debt investors to raise funds. In 2015, the company was registered as a sick unit with the Board of Industrial and Financial Reconstruction and in 2016, Patel — the founder and CMD — was on the banking industry’s wilful defaulters list.
- The listed shares of the company have been suspended from trading on the stock exchanges.
- With this acquisition, Reliance, for its part, will now get a foothold in the composites and carbon fibre business.
- Composites are used in a variety of applications and industries such as renewable energy, mass transportation, infrastructure and a host of other industrial products.
- Additionally, a key raw material for the business is petrochemicals, of which RIL is among the biggest producers in India.
- RIL is also investing in setting up India’s first carbon fibre manufacturing unit to cater to aerospace and defence needs.
- RIL is making low-cost and high-volume composite products like modular toilets, homes and composites for windmill blades and rotor blades.
- RIL has developed capabilities for 3D printing of wide-range of plastic and metals products for which it needs composites.
- RIL is developing new business verticals in the petrochemicals business to capture Rs30,000 crore composites market and has plans to produce graphene, enhanced plastics and elastomers, fibre reinforced composites which can replace steel.
- A composite is an engineered material made from two or more ingredients with significantly differing properties, either physical or chemical.
- One of the most common forms of composite in use today is carbon fibre. It is made by heating lengths of rayon, pitch or other types of fibre to extremely high temperatures in an oxygen-deprived oven.
- The resultant rayon strands are spun into a thread, then woven into sheets and mixed with hardening resins to form the various components needed.
- RIL is investing in India’s first and largest carbon fibre production line with its own technology — to cater to India’s aerospace and defence needs as well as the specialty industrial applications.
- Assets of Kemrock Industries have helped RIL to enter the composites business and is focusing on thermoset composites such as glass and carbon Fibre-Reinforced Polymers (FRPs).
- The ability to deliver exceptional strength (similar to or better than steel) at a significantly lower weight is a critical performance attribute of FRPs. Additionally, FRPs can withstand harsh weather, have a long life with minimal maintenance, are corrosion resistant and can be moulded into any shape.
- Composites are used in a wide range of markets and applications: industrial, railways, renewable energy, defence and aerospace.
- RIL expects the newly launched Reliance Composites Solutions (RCS) business to be the №1 composites player in India.
- RIL will focus on design and specifications driven markets and applications that have the potential to grant better returns. The focus areas include wind mill blades and parts for railways and metros, which have exacting standards of performance and safety (especially fire retardant).
- Also on the radar are carbon wraps to rehabilitate/refurbish India’s old infrastructure — bridges, buildings (for improved seismic performance) and pipes.
- RCS will design and administer low-cost and high-volume products such as modular toilets and homes to support the Swachh Bharat Mission, disaster relief measures and Housing for All programmes initiated by the Indian Government.
- Industrial 3D printing (especially with metal) is reaching an inflection point and the company has developed the capabilities to design and print a wide range of products using 3D printing technology — in both plastic and metal — from prototypes to functional parts.
Breakdown by Application, Composites has been segmented into
- Aviation
- Defence
- Shipping
- Mass Transportation
(Rail & Metro Rail) - Telecommunication
- Infrastructure & Disaster Management
- Oil & Gas
- Power & Renewable Energy
- Industrial & Municipal Piping
- Electricals & Electronics
- Automobile
- Relinforce (Structural Strengthening)
Composites Market segment by Manufacturing Processes Type
- Autoclave Moulding
- PREPREG Moulding
- RTM / VARTM
- Pultrusion
- General Moulding / Hand Lamination
- Vacuum Bagging
- Centrifugal Casting
- Filament Winding
- Layup
- Injection Molding
- Others
Composites Raw Material
Design Services
RIL VCD provides a number of services for composite industry having following functional capabilities :
- State of the art design studio for design and development to serve the customer needs from concept to commissioning
- Optimization of the design of products and structures, using 3D modeling and finite element analysis
- Material testing & characterization and modeling of composite material to predict accurate product behavior
- Complete range of manufacturing processes and raw material production to ensure correct product specification
- Reverse engineering and scanning facility
- Installation and commissioning
RelWoodTM — A material ahead of its time
- Our aim at Reliance was to bring India, a weather resistant and water proof product with a look and feel of precious wood especially suited for Indian climate. After more than 15 years of research by our technology partner Resysta, RelWood™ was developed, a material that is suited for Indian conditions and usage, preserves the environment and always features a consistent quality.
- Made with patented German technology it is a suitable alternative to wood. It is 100% waterproof, low maintenance, long lasting, recyclable and also thermoforming friendly.